What is Blast Furnace Slag and How to Process It?
The expanded slag ball is a porous lightweight slag formed by cooling the slag with high cooling water. The production methods include spray method, trench method and roller method. It can be used to make lightweight aggregate, inner wall panels, floors, etc. it can also be used in load-bearing structures. Blast furnace slag can also be used …
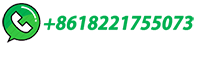