Vibrating Rotary Sintering Furnace
This vibrating rotary sintering furnace is for lithium battery positive and negative electrode materials, rare earth materials, magnetic materials, etc. Skip to content. We serve for material sciences and biotech. info@zylabsolution +86 371-86597277; We serve for material sciences and biotech.
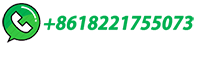