CO2 Emission Reduction in Blast Furnaces | SpringerLink
During blast furnace operations, many factors influence the behavior, and a serious selection of the independent variables affecting the productivity and the dangerous emissions has been performed. High productivity operation of a blast furnace requires enhancing reducibility and improving reduction behavior at high temperatures of sintered …
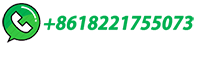