COMPARISON OF SINTER AND PELLET USAGE …
Specifically, the use of pellets results in a higher production of hot m etal per ton of. burden charged, lower slag ra te, lower coke rate and lower overall fuel consumption. The lower fuel con ...
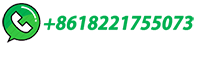
Specifically, the use of pellets results in a higher production of hot m etal per ton of. burden charged, lower slag ra te, lower coke rate and lower overall fuel consumption. The lower fuel con ...
pellets provide advantages to end users, such as improved productivity of blast furnaces, opportunity to increase the Fe content of the charge materials, and …
PMAI is the official industry body of Pellets Manufacturers in India. It was set up in 2013 with a fundamental premise to have a common forum for its members to share and exchange each other's views and problems, to promote and protect the interests of the Indian Pellet Industry. PMAI members include stand-alone Pellet plants as well units ...
During the blast furnace smelting process, the slag is required to have an appropriate melting temperature for ensuring a smooth operation of the blast furnace with low energy consumption [6,7].
SIMEC automatic rotary charcoal furnace is complete carbonization plant to process the biomass raw materials, such as sawdust, PKS (palm kernel shell), coconut shell, chicken litter, rice husk, peanut shell, crop stalk, log bark, sunflower shell etc, to be CHARCOAL with high fixed carbon via anaerobic destructive distillation. Working Principle:
2.1. Furnace thermal consumption monitoring. The thermal consumption of the traveling grate is evaluated. by the consumption of the added fuels, both in the pellet. and in the burners. The ...
There is no denying the fact that pelletizing will remain crucial in future for steelmaking in general and it can support the transition to green, carbon-neutral steel production. For this, the pelletizing …
Each pellet plant has customized the fluxed pellet chemistry to meet its customer's blast furnace operation. As a result, there are pellet plants producing as many as four grades of pellets. In North America, pellets have changed from a commodity in the early 1970s to a custom made product, meeting a customer's specific most demanding ...
The Travelling Grate Type Pellet Plant patent showcases MECON's focus on enhancing the efficiency and productivity of pellet production, contributing to the overall growth of the industry. Simultaneously, the patent for the Improved Blast Furnace design reflects MECON's dedication to advancing the capabilities of Blast Furnace technology ...
Taconite plants on the Iron Range — including U.S. Steel's existing one, Minntac, in Mountain Iron — primarily produce iron ore pellets that are used in traditional blast furnaces.
The pellets are used as raw material for Iron making in the plants as an alternate material for Sinter and/or Lump Ore. The pellets are preferred over sinter and lump ore as their shape, size, strength and excellent designed metallurgical properties in Blast …
objective is to transform the pelletized concentrate into hardened pellets that can be used as blast furnace feed or direct reduction furnace feed. has redesigned pallet car components to increase strength, stability and improved ... The pellet plants are running at full capacity with load and 99% availability. The indurating ...
The pellet-indurating furnace has self-regenerative gas flow, which leads to higher energy efficiency, thus resulting in lower consumption of fossil fuels. The consequence is the reduction in ...
Pellet cooling and handling – The pellets are cooled and screened after the induration. The over sized pellets are crushed and are sent along with the undersized to the stock house bins where they are reprocessed. Cooled pellets are sent to the storage for their transport to the downstream plants for further processing. Pelletization processes
During pellet making, the induration process influences the pellet properties. However, in an optimised pellet production plant, a good pellet induration is expected. . Figure 5 shows the effect of varying pellet basicity on the properties of pellets. It was observed that with the increase in the basicity particularly from 0.10 to 0.50, the …
26 Dec 2023, 1:49 pm. Synopsis. Sarda Energy and Minerals Limited (SEML) has received official approval from the Chhattisgarh state government to operate a larger capacity pellet plant. The ...
A technology assessment checklist that investors should consider when making a new pellet plant investment decision is presented. Schematic of the straight grate pelletizing process. Thermal ...
Operation. 's traveling grate pelletizing process consists of a green balling section where, after the mixing stage, green pellets are formed either by rolling on discs or in …
2.2 Laboratory Studies as per Pellet Plant Induration Furnace Operating Conditions Pelletization studies have been carried out on high alumina and high LOI iron ore nes as per present pellet plant indu-ration machine conditions (Table 4) to know the quality of the pellets. Table 3 Pellet green mix proportion Raw material % Iron ore nes 94.55
Circular Pelletizing Technology is designed for smaller production capacities, and the optimized arrangement of the circular furnace ensures an ultra-small footprint. Pellet pot testing facility for …
Circular Pelletizing Plant The building footprint of the induration furnace is significantly smaller compared with the straight grate process, which means that the world's most compact pelletizing plant – with its low building profile, short process air ducts, and standardized equipment - allows the cost of iron production to be slashed.
In case of failure of EOS, the situation of a (partially) closed sinter plant was tested. Purchased pellets replaced sinter, leading to a pellet and an 80% pellet/20% sinter trial. The trials were executed in the first half of 1994 at blast furnace No. 6, equipped with a PW-bell less top. Results are described.
3. Adopt unique smoke decontamination equipment so that the furnace is environmental-friendly. 4. High carbonization rate and high efficient. The carbonization rate is about 40-60% and the rate of finished production is above 95%. 5. Durable. The furnace are made of specific materials and can be used for 4 or 5 years. 6.
The Project. In 2018 was awarded the contract for engineering and equipment supplies for the PP#3 pellet plant at Vijayanagar; also delivered the wet grinding and filtration systems for this plant, which has a design capacity of 6.85 mtpa of blast furnace pellets.
Although direct reduction processes can operate with pellets having an iron content of 65% or lower, typical of blast furnace (BF)-grade pellets, the preferred feed for a DR plant has an iron content of 67% or greater. The …
The MIDREX® Shaft Furnace can use natural gas or a syngas from coal or coke oven gas as its reductant. MIDREX® Plants commonly operate in excess of 8000 hrs per year. In addition, the MIDREX® Shaft Furnace has been proven in using the widest variety of oxide pellets or lump ores to produce CDRI, HDRI and/or HBI.
The MIDREX® Process provides the most complete product dis-charge options commercially available with the flexibility to process iron oxide pellets and lump ores of …
Indian iron ores are suffering from high amounts of alumina and loss on ignition (LOI), which are deleterious constituents in both the pelletizing as well as iron making processes. Iron ore fines utilized in pellet making consist of alumina in the range of 3.20–3.35% and LOI in the range of 3.50–3.70%. Detailed palletization studies have …
It is worth mentioning that damp milling is usually used in small pellet plants using shaft furnaces with an annual capacity of 300,000–800,000 tonnes per annum to produce fired pellets with magnetite as the feed. However, damp milling is not suitable for pretreating hard hematite fines prior to pelletizing. 15.3.2.2. HPGR
Pellet plant Paradip Pellet plant Kirandul Beneficiation plant Dabuna Beneficiation plant Hazira Integrated steel mill Pune Downstream rerolling plant Potential construction ... Blast furnaces 2 units 7.0 MMT/Y 4,500m3/unitx 2 units Pellet plant 1 units 3.0 MMT/Y Sintering lines 2 units 6.0 MMT/Y
حقوق النشر © 2024.Artom كل الحقوق محفوظة.خريطة الموقع