Reducing energy consumption of a raw mill in cement industry
According to their study, the energy and exergy efficiencies are determined to be 84.3% and 25.2%, respectively. Atmaca and Kano glu [17] also studied the raw mill in cement industry. They ...
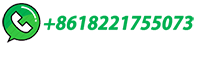