GLOBAL GYPSUM: GRINDING
GLOBAL GYPSUM: GRINDING Above right: One of the world's two largest gypsum mills. Both grind natural gypsum, one in Asia, the other in North America. Capacity = 94.5t/hr …
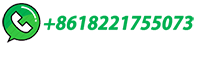
GLOBAL GYPSUM: GRINDING Above right: One of the world's two largest gypsum mills. Both grind natural gypsum, one in Asia, the other in North America. Capacity = 94.5t/hr …
A double belt conveyor feeds the gypsum into the raw material silo. This technique was chosen because it allows for the inclusion of flue-gas desulphurisation (FGD) gypsum at a later date. ... The static classifier is a proven technology for the grinding requirements of the gypsum wallboard industry. The fine particles pass out of the ...
The hammer mill, being a short-time calcining system, grinds, dries, calcines and classifies the raw gypsum in a single step. The resulting stucco is suitable for the production of plasterboard, gypsum fiberboard and gypsum wall blocks. A hammer mill can process moist FGD gypsum, pre-crushed natural gypsum, or a mixture of both.
Cement milling is the process of grinding together cement clinker, gypsum and other additives to produce a fine grey powder. The resulting material, called "cement meal", is then heated in a rotary kiln to around 2,000°F to produce the finished product known as Portland cement, which can be used for many different construction purposes.
Gypsum is an important industrial raw material. The gypsum powder ultrafine grinding mill is used for its deep processing, and the obtained gypsum powder can be widely used in construction, building materials, industrial molds, and art models, chemical industry, and agriculture, food processing, medicine and beauty, and other fields.
After grinding, the powdered raw mix, is stored in a raw meal-silo where blending takes place. Blending is done by injecting compressed air. Generally blending ratio is 1:10. ... Similarly, gypsum, fly ash and other additives are transported to their respective hoppers by belt conveyors. The proportioning of clinker, gypsum and HRS is done by ...
Thermal energy from process gases is used on Pfeiffer. Favorable control behavior. A short dwell time for the material to be ground along with remote control of grinding pressure …
We are operating a mill with lowest power i.e., 12.5 KWh/MT with 10 per cent on 90 micron for raw material grinding. • CPI & LNVT Ball Mill: CPI & LNVT is a renowned manufacturer of grinding equipment for the cement industry. Their ball mills are widely used for grinding cement clinker, gypsum and other materials into a fine powder.
Second stage: gypsum is crushed into particles smaller than 30mm, and transported to grinding mill. Third stage: separator delivers fineness-qualified raw gypsum powder into the furnace firing, the rest comes …
3. Grinding system: The gypsum raw material in the storage bin enters the mill through the vibrating feeder for finishing. An electromagnetic vibrating feeder is installed under the storage bin. This equipment is interlocked with the mill, and the supply of materials can be adjusted in real time according to the operation of the mill.
The mixture then sent to final grinding process. For ordinary Portland cement it remains between 3 to 4% and in case of Quick setting cement it can be reduced up to 2.5%. Role of Gypsum in Cement The main …
Grinding and calcining of gypsum with Pfeiffer grinding plants. 1 Two different modifi-cations of the hemihy-drate CaSO x 1⁄2. 4 H2O are produced. When gypsum is calcined in an atmosphere sat-urated with water vapour at an overpressure of several bars, a …
MPS 100 GC vertical roller mill for the grinding, drying and calcining of gypsum, Trevo, Brasil. MPS 3350 B mill for limestone grinding, China Chongqing Foreign Trade Huaneng, China. MPS 5000 B mill for raw material grinding, Turkey Tracim, Turkey. MPS 5300 B mill for cement raw material grinding, CDI Hail Cement, Saudi Arabia.
Calcining and Second Grind Raw gypsum rock is crushed before it arrives at the wall-board plant. Once there, it is heated to 350 F …
The PSD of the raw materials before grinding is presented in Figure S1 of the Supplementary Material. The 80th percentile passing size was used as the characteristic size to quantify the extent of the grinding operation and blend's grindability. ... Compressive strength is not reported for raw gypsum (C 0 G 100) and raw limestone …
Portland Cement is manufactured by adding 3% gypsum to clinker which is produced by grinding, pulverizing, mixing, and then burning a raw mix of silica, and calcium carbonate.
Process Flow Of Gypsum Grinding Line . Raw material: gypsum ; Capacity: 45-50 t/h; Feed size: <30mm; Discharge size: 120 mesh D80; Main equipment: LM170K vertical mill; Process Flow Of Gypsum Grinding Line. LM vertical roller mill - a comprehensive, large-scale grinding equipment that integrates the five functions of crushing, grinding, …
In the grinding stage the fineness most generally is turned out at 90-93% minus 100 mesh with a 325 mesh range of 30 to 50%. There are, of course variations depending upon desired end products and the physical characteristics of the raw Gypsum.
Jameson Simpson. Calcining and Second Grind Raw gypsum rock is crushed before it arrives at the wall-board plant. Once there, it is heated to 350 F in a process called calcining, which removes 75 percent of the molecularly bonded water. With this water removed, a second grind of the gypsum (which occurs during or after …
Here are the properties and benefits of Gypsum: Chemical formula Ca So4 2H2O, consisting of Sulfur hydroxide (SO3 46.5%) Calcium oxide (Cao 32.6% and water H2O 20.9%) Category: Raw materials. CONTACT US. The utilization of agricultural benefits. Gypsum can be used as a soil amendment for agricultural purposes by grinding …
Gypsum plays a very important role in controlling the rate of hardening of the cement. During the cement manufacturing process, upon the cooling of clinker, a small amount of gypsum is introduced during the final grinding process. Gypsum is added to control the "setting of cement". If not added, the cement will set immediately after mixing ...
This paper discusses the details of lab scale experimentation and interpretation of marsh cone test to assess the extent of gypsum dehydration, the paper also discusses the Plant scale application of the "Marsh cone flow test" for assisting the optimization of grinding parameters. 2. Raw materials used for Lab Scale Studies: The composition ...
Raymond Mill: Raymond mill is a popular choice for grinding gypsum into a fine powder. It operates by grinding the raw gypsum material between rotating grinding rollers and a grinding ring. The material is ground by pressure and friction, resulting in a fine powder with a relatively narrow particle size distribution.
Contribute to sbm2023/sbm development by creating an account on GitHub.
Steele Smooth Roll Crusher —Medium to fine grinding to produce discs, strips or sheets of material. The Steele Smooth Roll Crusher plays a key role in bulk raw material preparation, processing clays, coal fines, coke breeze and gypsum waste. Twin rollers reduce pebbles and plastic lumps to form thin, flat discs, strips or sheets of material ...
Above: MPS 225 B grinding-drying mill for natural and recycled gypsum. Capacity = 75t/hr Fineness = <10% R 0.150mm Power = 800kW Surface moisture (feed) = 8% Surface moisture (prod) <0.1%. Above right: One of the world's two largest gypsum mills. Both grind natural gypsum, one in Asia, the other in North America.
Mining limestone/raw materials; grinding, homogenisation, and blending various raw mix components; the preheater phase; processing and pyro processing in the kiln; ... Dry powder cement is anhydrous in nature when produced by grinding of clinker and gypsum. During the process of concrete mixing, water is added to develop concrete …
Ground granulated blast furnace slag (GGBS), desulphurization gypsum (DG), and phosphogypsum (PG), known as the common industrial wastes, were used in this study. Binders comprised of GGBS and waste gypsum were designed to develop a novel low carbon material; in order to promote the reactivity raw materials were processed by …
4. Grinding process. In the ball mill, the material is mainly crushed by impact and friction. In the vertical grinding mill, the material is mainly extrusion, and grinding is the auxiliary. The residence time of the material in the vertical mill is 2-3 minutes, while in the ball mill it takes 15-20 minutes.
The belt conveyor is used to mix and transport the cement clinker, gypsum, and mixture in a certain proportion. The cement roller press and cement mill are used to grind the cement raw material to the required particle size and packaging. There are two types of cement mill including a ball mill and vertical cement mill.
حقوق النشر © 2024.Artom كل الحقوق محفوظة.خريطة الموقع