Analysis and Optimization of Grinding …
Until now, various types of crushing equipment have been developed to meet the requirement of the industry, such as jaw crusher, cone crusher and vertical roller mill i.e., VRM [3,4,5]. Among these …
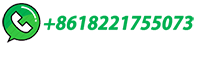
Until now, various types of crushing equipment have been developed to meet the requirement of the industry, such as jaw crusher, cone crusher and vertical roller mill i.e., VRM [3,4,5]. Among these …
A lowest mill motor vibration level of 1.42 mm/s2 occurred at an efficiency of 94.66% and the highest vibration level of 1.49 mm/s2 gave an efficiency of 93.72%. A lowest pinion gear vibration level of 1.025 mm/s2 recorded mill motor efficiency of 97.47% and the highest vibration level of 1.25 mm/s2 gave 94% efficiency.
The raw mill is either a Ball mill with two chambers or Vertical roller mill with inbuilt classifier. The hot gases from the pre heater enter the mill and are used for …
Vibration ball mill is a new type of high-efficiency and energy-saving grinding equipment. It has obvious advantages over traditional rotary ball mill in grinding fine and ultra-fine powder materials. The grinding efficiency of vibrating ball mill can be increased by 2-5 times, and energy consumption can be reduced by 20% – 30%.
MPS 3070 BK coal mill, Jaypee Cement Balaji, India. MPS 180 GC vertical roller mill for the grinding, drying and calcining of gypsum, Knauf Knin, Croatia. MPS 100 GC vertical roller mill for the grinding, drying and calcining of gypsum, Trevo, Brasil. MPS 3350 B mill for limestone grinding, China Chongqing Foreign Trade Huaneng, China.
May 14, 2013 •. 137 likes • 40,013 views. P. pradeepdeepi. Business Technology. 1 of 88. Download Now. Download to read offline. Vertical raw mill pradeep kumar - Download as a PDF or view online for free.
Hydraulic tension system: the hydraulic cylinder produces the pressure needed for the grinding roller to tighten, and the tension rod transmits the tension force of the hydraulic cylinder.The hydraulic cylinder is equipped with a nitrogen airbag to absorb the vibration of the raw mill during operation. Nozzle ring: located between the grinding table and the …
Vibrating mills are a type of grinding mill that uses a mechanical vibration to generate high-frequency oscillations and produce a fine grind in a short amount of time.Vibrating mills have several advantages over traditional grinding mills, including higher milling efficiency, reduced noise and vibration, and lower energy consumption.
Soft sensor enables computing parameters that can be physically impossible to measure. This work aims to develop a soft sensor for raw meal fineness in a vertical …
Vibration milling is a type of mechanical milling that utilizes vibrations to generate an impact force that breaks down particles into smaller sizes. This process is commonly used in various industries for material processing and synthesis.. Vibration milling is a milling process that uses the principles of mechanical vibration and impact to reduce the …
The particle size of the mill feed material and its size distribution impacts upon the performance of a vertical mill. • Abnormal feed size and/or distribution may increase the level of vibration and destabilize the mill. • Large feed size in any case will reduce the mill production rate. • Excess fines in the feed material or reject from ...
End milling is the operation of producing a flat surface which may be vertical, horizontal, or at an angle about the table surface. The cutter used is an end mill. The end milling cutters are also used for the production of slots, grooves, or keyways. A vertical milling machine is more suitable for end milling operations. #10 Saw Milling
cement ball mill. Application: limestone, clay, coal, feldspar, calcite, talc, iron ore, copper, phosphate, graphite, quartz, slag. Capacity: 0.65-615T/H. The cement ball mill usually can be applied to raw meal grinding or cement grinding. Besides, the cement ball mill also can be used for metallurgical, chemical, electric power, other mining ...
Vertical Slag Mill: A vertical slag mill is used for grinding and drying water quenched slag that is generated by blast furnaces into an active material which is then added to the finished cement. Note: Feed moisture <20%, feed size <10mm, final product moisture≤0.5%, final product fineness <4200cm2/g~5000cm2/g, power consumption …
During heat up there should be a sufficient air flow through the mill to force the heat transfer to the grinding part – forced convection. A sufficient air flow will result in a mill differential pressure of> 5mbar. The duration of heating should be at least until the temperatures after mill and after bag filter reach 85° C.
vibration vertical roller mill kind of vibration vertical raw mill operation /pdf/226 LMmaster for VRMs Epdf FOR VERTICAL ROLLER MILLS by Matthias Vertical raw mill pradeep kumar SlideShare May 15 Exception handling 21 vertical roller mill vibration is too large 1 Static separators Produce wide psd fineness adjustment byvanes cause .
The millstone wear will make the materials layer uninform and it also can make vibration. Operation problems. Grinding pressure is too high or the material layer is too thin will cause the vertical roller mill vibration problem. When you are operating the vertical roller mill, it needs a professional method or it will make the grinding roller ...
Preheater fan: The preheater fan is located at the top of the preheater tower and draws hot gases from the kiln. The. hot gases are used to preheat the raw materials before they enter the kiln ...
There are usually four kinds of VRMs in the cement production line, including raw meal mill, coal mill, Clinker Mill and cement mill, and the vertical mill occupies a large energy consumption unit. …
Abstract. This paper studies mathematical model of a Vertical Roller Mill (VRM). VRMs are widely used in cement, chemical, coal and electricity industries to …
Kind Of Vibration Vertical Raw Mill Operation Small cracker. Unlike milling in most other materials coolant is always recommended to assist in chip removal to control heat at the cutting edge and to prevent the re cutting of chips High pressure coolant (70 bar (1015 psi)) applied through the spindle tools is always to.Dear Analysts We are facing an issue on …
Vertical Roller Mills • Do not believe screen values unless you have checked them • Continuously change Process Parameters and document results to find Optimum • Optimum is highest capacity at lowest power consumption • Be sensitive to changes of feed material and adapt parameters • Focus on Relevant Process Parameters only • Optimize …
The vertical roller mill (VRM) is a kind of large equipment that widely used in cement materials industry. ... The dynamic characteristics of the above two sensing monitoring data were fused to judge the torsional vibration of mill drive system. ... (2, 4). Based on the result of differential operation, the ARIMA model is determined as ARIMA …
Regions of different types of vibration: ω = ω k / ω s 1, ω s 1 – first natural frequency of the strip, ωk – rolling stand second natural frequency. In white is marked the region with no vibrations, whereas in the black region the amplitudes of oscillations increase indefinitely. The different shades of gray starting with the less ...
A vertical roller mill (VRM) is a grinding equipment used for the size reduction of minerals, cement, and ceramics. The capacity of the VRM depends not only on the grinding material properties but also on the operational parameters of the VRM. This …
The vertical roller mill (VRM) is a type of grinding machine for raw material processing and cement grinding in the cement manufacturing process. In recent years, the VRM …
The raw vertical mill of CHAENG has stable operation, high output and convenient replacement of parts. It has been recognized and purchased by customers in South Asia, Africa and other markets: 1. A 5000t/d cement production line EPC turnkey project in South Africa adopts GRMR53.41 raw material vertical mill of CHAENG. 2.
The influence of materials on vertical mill vibration and the treatment method: it is mainly reflected in the particle size, the wearability and the moisture. In the vertical grinding operation process, to form a stable material layer, it is required that the grinding material has a suitable gradation, and more than 95% of the particle size is ...
Our expertise is built on Valmet's extensive engineering experience and knowhow. How is a vibration . vibration in raw mill. LOESCHEMILLS. kind of vibration vertical raw mill operation. Currently has a total of each type of raw material vertical mill 13, Common Failures and vertical mill operation. mill vibration causes and treatment. Request ...
A vibration mill is an important tool for achieving precise and efficient particle size reduction, grinding, and polishing of materials. Its unique approach to milling offers several advantages over other techniques, including high efficiency, uniform particle size distribution, reduced contamination, and versatility.
حقوق النشر © 2024.Artom كل الحقوق محفوظة.خريطة الموقع