Crushers
There are two basic types of jaw crushers: single toggle and double toggle. In the single toggle jaw crusher, an eccentric shaft is on the top of the crusher. Shaft rotation causes, along with the toggle plate, a …
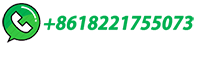
There are two basic types of jaw crushers: single toggle and double toggle. In the single toggle jaw crusher, an eccentric shaft is on the top of the crusher. Shaft rotation causes, along with the toggle plate, a …
Material Selection for Crusher Liners. The selection of material is made based on the types of crusher liners. When choosing a material, you should consider the strength of ore, size of feed material, and corrosion environment, etc. Here is a list of primary material used in crusher liners construction: Manganese Steel. It is one of the …
Cone Crushers. A cone (or "conical") crusher breaks down material with the use of an eccentric rotating head and a bowl. It is often used as a secondary or tertiary crusher. It is best for crushing material 200 mm and less. Advantages of a cone crusher include high productivity and low operating costs.
The crushability serves above all to determine the dimensions of the crusher and is only of secondary importance for the selection of the crusher type. The following tests and criteria give indications of the crushability: compressive strength/ Mohs hardness, "Bond impact crushing test" (2) and the "Los Angles Abrasion Test" (3).
life, but they also protect your crusher from peak crushing forces – resulting in an overall lower cost-per-ton advantage. Performance liner feed opening SHD-Fine SHD-Medium SHD-Coarse Max feed(B) Max feed(B) Max feed(B) R600 185 225 265 R900 190 225 245 R1100 190 225 285 B. Partnering for
The jaw crusher line is designed for the motor sizes listed in RPG and technical specifications. This means that for harder materials, the crusher will have to be operated at larger settings to avoid overload of drive and/or motor. Using oversized motors will lead to radically shorter crusher life and various mechanical problems.
CRUSHER SELECTION QUICK GUIDE. APPLICATION. mtrl. above 800 mtph 1. 5 Primary crushing, blasted, abrasive . mtrl. below 800 mtph 1.5 Primary crushing, blasted, abrasive . non-abrasive mtrl. 1.6 Primary crushing, blasted, . Secondary crushing, abrasive mtrl. …
No discussion of primary crusher selection would be complete without a comparison of the two leading types: the standard gyratory crusher and the Blake jaw crusher. Although their fields of application overlap to a considerable degree (at least in the realm of primary crushing) there is no real conflict between these two machines; one …
The selection of a crusher for tertiary crushing calls for both practical experience and theoretical know-how. This is where producers should call in an experienced applications specialist to make sure a …
The crushing station has two types: crawler type and tire type. Learn more about the Mobile Crushing Station. The mobile cone crusher is not restricted by the site. It can be easily and flexibly moved …
selection of the technological line structure for the b uilding aggrega tes PRODUCTION USING CENTRIFUGAL IMPA CT CRUSHERS DOI: 10.23968/2500-0055--32-37
See more on crushing-machine
WEBSelecting the right crusher for your operations. pcm_admin 19/03/2020, 10:25 pm. Perhaps the first and most fundamental aspects …
The installation process for jaw crusher plates typically involves the following steps: Remove the existing plates and clean the surface of the crusher. Place the new plates in position and secure them using the appropriate bolts and nuts. Check the alignment of the plates and make any necessary adjustments.
MANUAL CRUSHER SELECTION 1. Determine the maximum feed size. 2. The minimum feed size to the crusher, must always be less than 25mm (1"), in either open or closed circuit. 3. Determine the total tonnage throughput of the crusher: a) Open Circuit – Refer to capacity tables on previous pages, detailing maximum and minimum recommended …
parameters on-line. Original wear and spare parts – using origi-nal wear parts is the key to a successful crushing process. The design of our certifi ed wear parts starts with CAD simulations of the crusher cavity, which is the heart of the crush-ing process. By computer based planning and continuous quality control of the casting we
How you select your primary crusher will be based on factors like moisture content, maximum rock lump size, material density SG, abrasion index, degradability and it being prone to dusting or not. The …
sbm design and selection of crusher for bulk materialDesign Of Sand Belt Conveyor Details Design Belt Conveyor Belt Conveyors Taylor Automated Material Handling.Slider bed belt co
I proposed this literature from to help him select a jaw liner set. Designing your jaw crusher liners for the right function starts with asking 'what final product crush size distribution do I want' & 'what …
Primary Crusher Selection & Design. How you select your primary crusher will be based on factors like moisture content, maximum rock lump size, material density SG, abrasion index, degradability and it …
A number of factors go into the proper selection of a crusher for a given application including the following. Below are some important criteria to consider when selecting a lump breaker: Whether the crusher handles the maximum required capacity to be processed without undue strain or overload. Whether the machine handles the …
40-60% passing the midpoint. 0-10% passing the closed-side setting. A well-graded feed to the Cone Crusher. You want to match the entire feed gradation, not just the feed size, so that you utilize ...
Stone crusher plant design is a crucial factor in the efficient operation of the crushing process. The primary goal of plant design is to achieve the desired product size and capacity while balancing capital and operational costs. A well-designed plant will help minimize production downtime and reduce operating costs while maximizing production ...
The crusher is a machine that is designed such that to reduce the size of large rocks into smaller rocks like gravels. It is not only for that, but it is also used for recycling of the waste materials. Crusher is a multi-dimensional machine. Crusher has the ability of changing the form of material. In rock ores, crusher is used for the ...
Show all Crushers Manufacturers. Industrial crushers reduce large rocks, ore, or waste materials to smaller sizes. They are the first level of size reducer; further granularization …
There are several types of industrial crushers available to industrial buyers. These types include: Cone or gyratory crushers insert feed via a cone-shape bowl and crush it with a spinning or gyrating head. HPGR (high pressure grinding rollers), roll/roller crushers, or mineral sizers use two large rollers or a roller and a flat surface.
The selection of a crusher for this job requires practical experience and theoretical knowledge. This is where the AIShred can help. The user will have to choose between the two main types of crushers for fine crushing and cubicising – i.e., cone and impact crushers. The decisive factors for selection of the most appropriate equipment are the ...
Mellott has the expertise to properly size and select the optimal cone crushers for your purposes. Contact us today at 888.621.8533 or online to discuss how we can maximize your cone-crushing productivity. This entry was posted in …
In this article, we show you how to choose plastic crushers. 1. How to Feed. There 3 ways of feed a crusher by hands, by conveyor and by forklift. The latter 2 options concern machines so they can transport heavy materials in a bulk. Still, take special care of no metal can mix with the infeed materials. Manual feed is direct and simple.
Blake jaw crushers, also as double toggle jaw crushers, are characterized by the position of the pivot of the swing jaw, which is located at the top of the machine. This design allows for a larger feed size and a higher capacity, making it suitable for primary crushing. The motion of the swing jaw in a Blake crusher is predominantly vertical ...
Crushing Equipment Selection. In open pit quarry operations the loading of the blasted rock for transportation to the primary crusher house involves either power-shovels. Any size of primary crusher may be used for hand-loaded rock; it all depends upon how much secondary shooting, and hand sledging, the operator feels he can afford. So …
حقوق النشر © 2024.Artom كل الحقوق محفوظة.خريطة الموقع