CNC Guide (Part 1): Best Design Practices for Custom
Material Selection. Material selection is critical in determining the overall functionality and cost of the part. The designer must define the design's important …
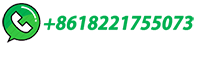
Material Selection. Material selection is critical in determining the overall functionality and cost of the part. The designer must define the design's important …
Theoretical design and material selection: The materials for the construction of the modified cassava milling machine are: the shaft, pulley, belt, electric motor,
Choosing a machine spindle interface is a key decision, as this often defines the limitations on metal-cutting efficiency. There is no quick answer to which interface is best—it really depends upon the components to be machined and the operations being carried out. It should not be assumed that the standard spindle options with a machine are ...
Design guide for CNC Milling. July 22, 2016. Steven Weinberg. CNC milling is the most common fabrication method for professional prototyping, scaling well into the low- to mid-volume levels and sometimes higher. As with any manufacturing process, the more familiar the designer is the better and easier to produce the part will be.
Design considerations, material selection, tool choice, and design optimization allow for customization of CNC machining to meet specific needs and …
They are capable of cutting a variety of materials, from plastics and composites to metals and alloys. Typically, CNC milling technology can create parts with tolerances as tight as ± 0.001 inches to ±0.005 inches. However, the CNC milling machine must be highly accurate and precise to achieve these tolerances.
Technological parameters. The technological parameters of milling include: rotational speed n [rpm]; diameter of the tool D c [mm]; cutting speed v c [m / min] – equation 1; feed speed v f [mm / min] – equation 2; feed per revolution f f [mm / rev]; feed per blade / tooth f z [mm / tooth] – equation 3; width a e and depth of cut a p [mm].
The first step in narrowing material selection, is to prioritize your part's requirements, keeping in mind issues such as environmental factors, mechanical elements, cosmetic considerations, part size, cost, and, as seen here, electrical factors such …
First, consider its size. If you will be working with large or heavy pieces of material, you'll want a larger milling machine so that you can properly accommodate their size. If you plan on using smaller pieces more regularly, opt for a smaller machine. Second, look at the power and speed of the machine.
They are usually chosen when the customer has very low production runs associated with the project. Chrome-moly materials range (from 4130, P20, 4140 and etc.) have a hardness range from 28-34 HRC and have good mechanical properties. They are ideal for cavity and core plates as well as other plates required in the mold base.
CNC milling is a manufacturing process that involves cutting and shaping materials by utilizing various cutting tools to remove the material, whereby the desired shapes and features are imparted into the workpiece to achieve the engineered design. All computer-controlled milling machines, some referred to as machining centers, are …
Categories#6: Form Milling Cutters. This is a cutter used for shaping irregular contours, both 2D and 3D. These cutters also come in different configurations and shapes. It is ideal for creating helical gears and other complex and intricate surfaces. It is used for groove, chamfering, and full-radius milling.
Besides the primary components, a CNC milling machine necessitates secondary yet crucial parts that control the cutting tool's movement, support the arbor, and secure the workpiece during machining. ... CNC machining can be customized by taking into account design, material selection, tool selection, and design optimization to …
As the number of alternative machines has increased and their technology has been continuously developed, the machine selection problem has attracted many researchers. This article reviews recent …
Milling Machine Definition: The milling machine is a type of machine which removes the material from the workpiece by feeding the work past a rotating multipoint cutter.The metal removal rate is higher very high as the cutter has a high speed and many cutting edges. It is the most important machine in the tool room as nearly all the …
Therefore, this paper will focus solely on the design of a low-cost CNC milling machine using Arduino technology and stepper motors. The rest of the contribution is organized as follows: in Sect. 2 the design method; in Sect. 3 the selection formulation; Sect. 4 describes the results; and finally the conclusions are presented in Sect. 5 .
The limitations of significant tool wear and tool breakage of commercially available fluted micro-end mill tools often lead to ineffective and inefficient manufacturing, while surface quality and geometric dimensions remain unacceptably poor. This is especially true for machining of difficult-to-machine (DTM) materials, such as super …
Therefore, the material selection is the primitive factor in machine tool design. Generally, metallic structures possesses low damping performance due to lower damping capacity [28]. Cast iron has ...
Teflon (PTFE) Polytetrafluoroethylene, commonly known as Teflon, is a popular polymer. It is a hydrophobic material unaffected by water or water-based liquids. It has an extremely low coefficient of …
Material Selection for CNC Milling Tools. Carbon Steel. High-Speed Steel (HSS) Carbide. Workpiece Material. Machining Operation. Tool Geometry. In the realm of manufacturing and metalworking, CNC (Computer Numerical Control) milling stands out as one of the most vital processes. At the heart of this technique lies a variety of tools, each ...
The most common type of motor used in high-speed motor spindles is an AC induction motor. In this design, the rotor is attached to the spindle shaft, either with an adhesive or thermal clamping. The rotor and stator, the winding in which the rotor revolves, are generally provided by a motor or drive supplier.
For a hobbyist desktop mill, a solid machine costs roughly $2,500 to $7,500. CNC knee mills start at $15,000 and go up to $75,000. 3-Axis Mills begin around $45,000 and go as high as $100,000. Production mills and lathes are $250,000 and up, depending on size and features.
The CAD data is translated into a cutter path and tool selection program, using computer-aided manufacturing (CAM) software. The CAM software takes the 3D model and generates G-code. The form milling cutter is loaded into the CNC milling machine, along with any required standard cutters. The workpiece or billet is set up on …
Milling Machine Classification. In general terms, milling machines can be classified by the orientation of their spindle (or spindles, in the case of multi-spindle machining centers). In most cases, this is either horizontal or …
3. Tips for Optimizing Material Selection for CNC Machining. 4. Which is the Best Material For a CNC Machining Project? 5. Conclusion. 6. Frequently Asked Questions (FAQs) The CNC machining …
CNC milling is a manufacturing process that uses computer-controlled toolpaths to machine metal, plastic and other materials in different shapes and parts. The milling machine is controlled by a computer program that translates digital design files into commands for the machine to follow. CNC milling started gaining popularity in the ...
CNC Plastics Selection Guide. The first step in designing a part is to determine what material it should be made out of. If you decide the part should be plastic, and it should be CNC machined, the selection does not simply stop there. There is a plethora of machinable plastic to choose from for plastic machining in 2022, each with its own ...
The process of experimental design; a selection of parameters and details of ... in this section as well. Finally, this work will end up with the conclusions in Sect. 5. 2 Experimental methodology. 2.1 Selection of materials and machining setup. Hardox 600 is selected as the workpiece for this study. ... The milling machine is the conventional ...
Click the above image to view the Material Selection Chart When choosing materials for the structures and especially the motion-related components on a machine or a piece of assembly equipment, the physical properties of those materials are vitally important to the overall life of the end product.
Common screen types. Three main types, or profiles, of screens are used in milling machines: 1) round hole screens, 2) slotted or herringbone screens and 3) conidur screens (Figure 2). Round hole screens are by far the most common. These screens are created by stamping circular holes into a steel sheet. The holes are arranged in rows, …
حقوق النشر © 2024.Artom كل الحقوق محفوظة.خريطة الموقع