sound-transmitter-ball-mill-level-sensor.pdf
PEPL PEPL INTRODUCTION The Electronic Ear type PI 213 is a magnetic Sensor also know as Sound Transmitter, which is using the mill shell as Membrane. This means the Sensor is only detecting the mill shell vibrations, caused by the Grinding balls hitting the mill lining and material in the mill, and so the Pyrotech Noise Level Sound Transmitter …
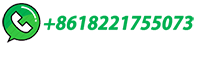