(Video) How Cement Is Made
6. Raw material mill. This takes places in vertical steel mill, which grinds the material through the pressure exerted by three conical rollers. Which roll over a turning milling table. Horizontal mills, inside which the material is pulverized by means of steel balls, are also used in this phase.
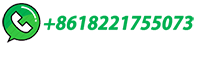