Four Points To Improve Tin Ore Flotation …
Recovery is the percentage of valuable minerals successfully extracted from ore during the flotation process. During the flotation process, the pH value of the solution, particle-bubble interaction, metal …
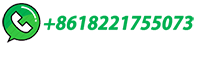