Ore Processing | Multotec
Mineral & Ore Processing. Ore processing is a chain of processing applications which treats run of mine to firstly high-grade concentrate (concentration of ores) and then to the pure mineral or metal. The refined ore is used in manufacturing equipment and machinery in numerous industries, or is for sale in industry, commerce and consumer ...
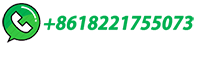