Forged Steel Ball
Each FOX Forged Steel grinding ball is solid from surface to center. This is a forged steel ball that is through hardened for superior strength. These sturdy, well built, shock-absorbing steel balls are the perfect hardness for ball mill grinding. Whether you are grinding raw materials in ball mills, or using planetary ball mills on a smaller ...
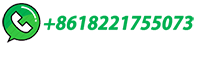