Zr-substitution in LaNi5-type hydride compound by room temperature ball
High-energy ball milling at room temperature has been used to prepare the pseudo-binary compound La 1−x Zr x Ni 5 (x =0.5) in amorphous state. The stability of this phase has been investigated by XRD, DSC and DTA.It starts to crystallise into single-phase La 0.5 Zr 0.5 Ni 5 alloy at 361 °C and undergoes decomposition into LaNi 5 and ZrNi 5 …
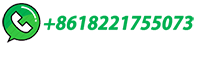