SAG MILL DISCHARGE SCREENS-TROMMEL vs. …
Screen panel size is 28 by 54 inches. The oversize return tube turns with the trommel These things are not small. The diameter of the trommel for the 34-foot mill is 13.5 feet and the screen surface length is almost 13 feet. This gives us about 550 square feet of screen area, for roughly 30,000 tons a day or 1,300 tons an hour.
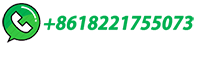