(PDF) Prediction of grinding force in microgrinding of …
PDF | This study investigates grinding force prediction in microgrinding of ceramic materials by cohesive zone method (CZM) and finite element analysis... | Find, …
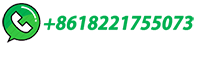
PDF | This study investigates grinding force prediction in microgrinding of ceramic materials by cohesive zone method (CZM) and finite element analysis... | Find, …
MICROGRINDING OF CERAMIC MATERIALS by Jie Feng A dissertation submitted in partial fulfillment of the requirements for the degree of Doctor of Philosophy (Mechanical Engineering) in The University of Michigan 2010 Doctoral Committee: Professor Jun Ni, Chair Professor Yogesh Gianchandani Professor Xiaoqing Pan Professor Albert Shih
[25] J. Feng, B.S. Kim, J. Ni, Modeling of ceramic microgrinding by cohesive zone based finite element method, in: Proceedings of the ASME 2009 International Manufacturing Science and Engineering ...
Cohesive Zone Models (CZMs) are well suited for modeling adhesives. In this paper a tri-linear, strain-rate dependent CZM is presented. This model is compared to the bi-linear, strain-rate independent model implemented in ABAQUS TM. The parameters of these models are determined by direct testing of tensile bulk, tapered double …
Modeling Of Ceramic Microgrinding By Cohesive . Based on cohesive zone finite element analysis, this study investigates grinding force modeling and prediction in ceramic microgrinding by modeling the actual chip generation process The chip generation is explicitly simulated based on actual diamond cutting edge profile
Feng et al. [131, 132] used cohesive zone method (CZM)-based finite element analysis (FEA) model to achieve an explicit modeling of fracture. Surface chipping depth was predicted from the fully ...
The DCB specimen is sketched in Fig. 1 (a); and the cohesive zone model with an arbitrary traction-separation law σ(δ) and progressive failure are illustrated in Fig. 1 (b). h and B are the height and width of substrates, respectively; v denotes the applied displacement at the loading rod; a 0 is the initial length of crack and δ T0 denotes the …
@inproceedings{Feng2009ModelingOC, title={Modeling of ceramic microgridning by cohesive zone based finite element method [microgridning read microgrinding]}, …
Nonlinear cohesive zone model3.1. Kinematics of the interfacial surface. Considerably less work has been spent on the cohesive model at finite deformations. The reason is the complexity of the kinematics of the interfacial surface and the interface traction–separation relation, such as inelastic constitutive equations and the damage …
Modeling complex crack paths in ceramic laminates: A novel variational framework combining the phase field method of fracture and the cohesive zone model February 2018 Journal of the European ...
The chip thickness model is then implemented in FEA to predict peak grinding force in grinding alumina. The simulation result is compared with experimental result for a specific diamond on the microgrinding tool. The feasibility of modeling ceramic microgrinding by CZM based FEA is then discussed.
[25] J. Feng, Kim, J. Ni, Modeling of ceramic microgrinding by cohesive zone based finite element method, in: Proceedings of the ASME 2009 International Manufacturing Science and Engineering Conference, 2009.
This study investigates numerical modeling of surface generation in microgrinding of ceramic materials by coupled trajectory and finite element analysis. The resultant surface generation from ...
Abstract. This study investigates numerical modeling of surface generation in microgrinding of ceramic materials by coupled trajectory and finite element analysis. …
Based on cohesive zone finite element analysis, this study investigates grinding force modeling and prediction in ceramic microgrinding by modeling the …
The cohesive zone model implies that normal stress continues to be transferred across a discontinuity which may or may not be visible as shown in Fig. 6.1. This stress is determined from the softening stress–strain relation that various rocks exhibit in calibrations tests. This transferred normal stress is a function of the separation and ...
WebSep 01, 2012 J. Feng, B.S. Kim, J. Ni, Modeling of ceramic microgrinding by cohesive zone based finite element method, in Proceedings of the ASME 2009 International Manufacturing Science and Engineering Conference, 2009. 29-Aug-2021. 692 COM. Read More. modeling of ceramic microgrinding by cohesive zone b.
ORIGINAL ARTICLE Prediction of grinding force in microgrinding of ceramic materials by cohesive zone-based finite element method Jie Feng & Peng Chen & Jun Ni Received: 22 December 2012 /Accepted ...
Abstract. This paper reviews the cohesive process zone model, a general model which can deal with the nonlinear zone ahead of the crack tip––due to plasticity or microcracking––present in many materials. Furthermore, the cohesive zone model is able to adequately predict the behaviour of uncracked structures, including those with blunt ...
Section snippets Semiempirical heat flux model for biobone ductile microgrinding. At present, the heat flux calculation method commonly used by researchers is [31,32] q = W S = F t v s l c b, where W is the grinding work, and S is the contact area between grinding wheel and the workpiece. F t is the tangential grinding force, v s is the …
Modeling of Ceramic Microgrinding by Cohesive Zone . 2010920 Feng, J, Kim, B, Ni, J. "Modeling of Ceramic Microgrinding by Cohesive Zone Based Finite Element Method." Proceedings of the ASME 2009 International . اObtener precio
Journal of the American Ceramic Society (JACerS) is a ... Cohesive zone FEM is used to study these regimes for different indenter geometries. In a three-dimensional model, the median/radial cracking is considered by introducing cohesive element planes that are aligned along the indenter edges perpendicular to the indented …
the reaction force on the indenter during fracture, and this is important for modeling the machining force in grinding ceramic materials. Figure 2-2 Scheme of fracture in …
For example, a functionally graded armor composite with a tailored ceramic to metal through-thickness gradient combines the beneficial effects of ceramics (e.g., hardness) and metals ... In this section, the cohesive zone model is employed to study a mixed-mode dynamic crack propagation problem, where the cohesive elements allow …
in microgrinding of ceramic materials by cohesive zone method (CZM) and finite element analysis (FEA). Based on detail abrasive cutting edge profile and maximum chip thickness analysis in microgrinding, a CZM-based finite element model is developed to predict grinding force in microgrinding of Alumina. The simulation result is com-
Based on cohesive zone finite element analysis, this study investigates grinding force modeling and prediction in ceramic microgrinding by modeling the actual chip generation process. · J. Feng, B.S. Kim, J. Ni, Modeling of ceramic microgrinding by cohesive zone based finite element method, in: Proceedings of the ASME 2009 ...
Highlights. •. Cohesive zone modeling is used to simulate the dynamic impact failure of adhesives. •. Interplay between critical energy release rate and adhesive thickness is considered. •. A thicker adhesive decreases armor performance but reduces the ceramic damage area. •.
This study investigates modeling of microgrinding of ceramic materials by cohesive zone method (CZM) and Finite element analysis (FEA). A maximum grinding …
The feasibility of force prediction in microgrinding of ceramic materials by CZM-based FEA is discussed and proven promising. This study investigates grinding …
This study investigates numerical modeling of surface generation in microgrinding of ceramic materials by coupled trajectory and finite element analysis. The resultant surface generation from both ductile flow mode grinding and fracture mode grinding is ...
حقوق النشر © 2024.Artom كل الحقوق محفوظة.خريطة الموقع