Trivalent and Pentavalent Antimony
Volatilization roasting of typically antimony(III) stibnite ores with charcoal or coke at temperatures over 1000 °C, a dominant process for 5–25% antimony ore/concentrates (Anderson, 2012), results in direct recovery of antimony oxides from the produced vapour phase. The production of antimony ...
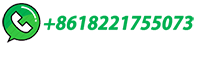