Gyratory Crusher (Gyratory Crushers Explained)
Gyratory crushers are always installed vertically orientated. A gyratory crusher's size is classified by: Its gape and mantle diameter. The diameter of the receiving opening. …
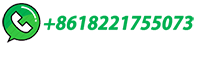
Gyratory crushers are always installed vertically orientated. A gyratory crusher's size is classified by: Its gape and mantle diameter. The diameter of the receiving opening. …
The Gyratory Crusher TS is distinguished from other gyratory crushers by its revolutionary design which allows you to easily and safely perform major service and maintenance functions. It is designed so that you can easily access and remove the eccentric assembly, bushings and hydraulic piston through the top of the crusher, hence the name ...
DOI: 10.1016/j.mineng.2024.108606 Corpus ID: 267639478; DEM simulation and optimization of crushing chamber shape of gyratory crusher based on Ab-t10 model @article{Guo2024DEMSA, title={DEM simulation and optimization of crushing chamber shape of gyratory crusher based on Ab-t10 model}, author={Jianbo Guo and Guoqiang …
1. Crusher capacity calculated based on a feed material bulk density of 1.6 metric t/m³. Actual values depend on feed material characteristics and crusher configuration. All data should be used as a guide only and are not guaranteed. 2. For larger feed opening a Double Mouth Spider is available on request. Recommended maximum feed size up to …
In a cement manufacturing unit, 36 tonne/h of calcite of 5-cm size is fed to a gyratory crusher. Screen analysis from the crusher shows a surface area of product of 61.7 m2/kg. Thecrushed material is then subjected to fine reduction in a hammer mill. Mill product analysis indicates a surface area of 740 m2/kg. Rittinger s number for calcite is 75.9
The original productivity of simulation is 1579 t/h, which is consistent with the actual productivity (1430 t/h-2970 t/h) [32], the validity of the established DEM model of gyratory crusher is preliminary verified, furthermore, the corresponding crushing force is 3.11 × 10 8 Pa, and the discharge granularity is 59.67.
Hydraulic separation and individual lifting of shells for easy & safe maintenance. 70% reduction in downtime with new set of shells and concaves. Significant reduction of …
In a cement manufacturing unit, 36 tonne/h of calcite of 5-cm size is fed to a gyratory crusher. Screen analysis from the crusher shows a surface area of product of 61.7 𝑚2/𝑘𝑔. The crushed material is then subjected to fine reduction in a hammer mill. Mill product analysis indicates a surface area of 740 𝑚2/𝑘𝑔.
2. GYRATORY CRUSHERS. The original patent for the gyratory crusher was granted to Phile- tus W. Gates in 1881. This fint crusher was used by the Buffalo Cement Co. At the time these early gyratory crushers were developed all mining and quarrying, either underground or open pit, was done by hand; tonnages generally were small and product ...
Gyratory crushers. State-of-the-art technology with throughput rates of up to 14,000 t/h. 2. Our solutions for the hardest jobs. 3. Fields of application and design characteristics. …
CG800i crushers offer excellent reliability and safer & faster maintenance – up to 30% faster than competing crushers. A robustly designed one-piece main shaft and …
The majority of gyratory crushers are used as primaries, i.e. they receive the initial feed from the mine or quarry. The same type of crusher with chamber modifications is used as a secondary crusher, particularly when following a large primary crusher. The fine-reduction gyratory crusher can also be used for tertiary crushing.
1. Crusher capacity calculated based on a feed material bulk density of 1.6 metric t/m³. Actual values depend on feed material characteristics and crusher configuration. All data should be used as a guide only and are not guaranteed. 2. For larger feed opening a Double Mouth Spider is available on request. Recommended maximum feed size up to …
Question: 3.5. Trap rock is crushed in a gyratory crusher. The feed is nearly uniform 2-in. spheres. The differential screen analysis of the product is given in column (1) of Table 28.4. The power required to crush this material is 400 kW. Of this 10 kW is needed to operate the empty mill. By reducing the clearance between the crushing head and ...
Gyratory Crushers Jaw Crushers Impact Crushers; Typical rules for primary crusher selection: Rule 1: Always use a jaw crusher if you can due to lower costs. Rule 2: For low capacity applications, use jaw crusher and hydraulic hammer for oversize. Rule 3: For high capacities, use jaw crusher with big intake openings.
A gyratory crusher is one of the main types of primary crushers in a mine or ore processing plant. Gyratory crushers are designated in size either by the gape and …
Comminution by gyratory crusher is the first stage in the size reduction operation in mineral processing. In the copper industry, these machines are widely utilized, and their reliability has become a relevant aspect. To optimize the design and to improve the availability of gyratory crushers, it is necessary to calculate their power and torque …
The gyratory crusher operates by means of a gyrating mantle, which gyrates continuously against a stationary concave surface. The main components of a gyratory crusher include the mantle, the concave surface, and an eccentrically mounted rotating shaft. The mantle is located on the top of the shaft and is connected to it via a …
The gyratory crusher model is PXZ1417, and its specific structure is shown in Fig. 1. The crusher is composed of external shell, mantle shaft, sliding bearing, friction disc and other parts. The sliding bearings include the beam bushing, eccentric bushing, and frame bushing. The failed component in this case is the eccentric bushing.
Above crushing rates of 900 t/h, gyratory crushers are almost always used. Gyratory crushers are relatively sensitive to moist feed material, as the crushing gap is likely to …
Since H-E Parts improved the material selection and implemented a mantle and concave redesign, the following has been achieved: Full 12-month concave life over a four-mantle set, with a …
Capacity (by hour) 1,300 - 2,700 mtph (1,430 - 2,970 stph) Feed opening. 1,067.0 mm (42.0 in.) Motor power. 315 kw (430 hp) CG810i crusher is built to be robust, reliable and efficient. Connected to SAM by , they revolutionize availability and optimize uptime by giving you actionable insights into how the crusher is performing.
Question #210484. In a cement manufacturing unit, 36 tonne/h of calcite of 5-cm size is fed to a gyratory crusher. Screen analysis from the crusher shows a surface area of product of 61.7 m2/kg. Thecrushed material is then subjected to fine reduction in a hammer mill. Mill product analysis indicates a surface area of 740 m2/kg.
CG830i. Capacity (by hour) 2,700 - 6,000 mtph (2,980 - 6,610 stph) Feed opening. 1,525.0 mm (60.0 in.) Motor power. 660 kw (885 hp) CG830i crusher is built to be robust, reliable and efficient. Connected to SAM by , they revolutionize availability and optimize uptime by giving you actionable insights into how the crusher is ...
Gyratory Crusher - Mining Fundamentals. A gyratory crusher is an ore processing machine that crushes the ore between an eccentrically mounted cone and a crushing throat, that is fixed. In mining, the most important criteria for effective crushing of ores is to choose the type of crusher that suits the rock (ore) material, and to ensure uniform ...
FULLER-Traylor gyratory crushers have been delivering at the highest level in some of the world's harshest environments, ensuring optimised and consistent throughput, with maximised uptime, to the mineral processing industry for over 50 years. The long operating life of the FULLER® HD gyratory crushers can be attributed to the robust, hard ...
The core of the Superior™ MKIII 54-75 primary gyratory crusher is the robust design. Resistant U-shaped arched spider, durable manganese bronze spider bushing, new shell separators and inspection ports, as well as hardy one-piece main shaft makes the Superior™ MKIII 54-75 primary gyratory crusher efficient and lasting, but easy to …
Key Benefits. Ultra heavy-duty design. Lowest total cost of ownership. Lowest cost per tonne in operation. Digitally enabled. Safer, simpler maintenance. Turn on sound. Crush even the most challenging ore with the digitally-enabled TSUV gyratory crusher and achieve the lowest total cost per metric tonne in operation.
A primary gyratory crusher was required to crush iron ore at the rate of 3000 t/h. The largest size of the run-of-mine ore was 1000 mm. The required product size was less than 162 mm. Manufacturer's data indicated that the nearest size of gyratory crusher would be 1370 mm × 1880 mm with a cone angle of 18°.
Gyratory crusher is a crushing equipment that uses the gyratory motion of the crushing cone in the conical cavity inside the shell to extrude, bend, and impact …
حقوق النشر © 2024.Artom كل الحقوق محفوظة.خريطة الموقع