Common Iron Ore Crushing and Screening Process – …
The three-stage open circuit process is used to process argillaceous iron ore with high water content and large and medium-sized iron ore concentrators that are prone to produce a large amount of quartz dust ore. Its advantage is that it can simplify the equipment configuration of the crushing workshop and reduce the capital construction ...
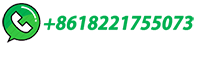