(PDF) ROCK BLASTING FOR MINING
ROCK BLASTING FOR MINING. Prof. A. Balasubramanian. Centre for Advanced Studies in Earth Science. University of Mysore. …
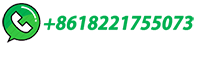
ROCK BLASTING FOR MINING. Prof. A. Balasubramanian. Centre for Advanced Studies in Earth Science. University of Mysore. …
Database and statistical analysis In this research work, the data from six limestone mines in Iran was collected to predict and validate the GEP and ANN models. Table 1 shows the geographical coordinates and specifications of these mines. In order to obtain the real data, the BC data of six limestone mines from 2011 to November 2018 was collected.
The current techniques used for monitoring the blasting process in open pit mines are manual, intermittent and inefficient and can expose technical manpower to hazardous conditions. This study presents the application …
Under well-controlled conditions, Ouchterlony et al. [] assessed energy partitioning of limestone production blasts and computed in-hole losses, seismic energy, the kinetic energy of throw, and fragmentation energy.Their search revealed the energy partitioning of a blast with bulk emulsion explosive would be []Crushing and other losses …
The cyclic load generated by the blasting vibration in the mining process has a significant degrading effect on the slope rock mass. To clarify the cumulative damage evolution of the microcrystalline limestone under the cyclic blasting load, the microcrystalline limestone in the Zhujiapo mining area in Sichuan Province is used as …
It is very important to predict the blasting fragmentation size of fractured rock mass. Based on the geological conditions of practical engineering rock mass, a plane analysis model of bench blasting in layered rock mass considering microcrack structure was established. And the distribution law of stress in the bench blasting of layered rock …
Blasting cost prediction and optimization is of great importance and significance to achieve optimal fragmentation through controlling the adverse consequences of the blasting process. By gathering explosive data from six limestone mines in Iran, the present study aimed to develop a model to predict blasting cost, by gene expression …
Limestone mining isn't discussed as often as, say, fracking or oil drilling, but it has its fair share of risks and problems. Let's look at six top limestone mining issues. 1. Groundwater Contamination. Limestone is mined underground, but vital groundwater is located underground too. When there is a limestone mine near a groundwater source ...
Underground mining of limestone has some advantages over surface quarrying and will probably increase in the future. Typical public concerns about limestone mining include dust, noise, blasting vibration, and truck and other traffic associated with quarry operations. Some limestones are also aquifers, that is, they are rock units that can yield ...
146 blasting data from six limestone mines in Iran using the artificial neural networks (ANNs), gene expression programming (GEP), linear multivariate regression (LMR), and ... first step in the production process in open-pit mines and the cost of this step is 8-12% of the total mining costs [8], and lack of any study in the ...
During blasting operations in open pit mines, most of the blast energy (approximately 40%) is wasted due to ground vibration. This phenomenon causes damages to the surrounding structures and pit ...
Blasting, Vibration, AlvandQoly, Limestone Mine, Analysing . 1. Introduction measurement of ground vibration considered potentially . In most of surface mines, blasting operation is the first element of the ore extraction process. The primary purpose of blasting is rock fragmentation and displacement of the broken rock.
RANJIT PASWAN. This paper deals with the controlled blasting techniques implemented to control overbreaks, blast induced blast vibration and to aid in the stability to the rock mass of highwall at Jayant Opencast Project of …
1. Introduction. Mining activity is mostly represented by these four main operations: drilling, blasting, loading and hauling. For a proper mine planning and design, all of these operations need to be carefully planned in such a manner that can prevent extra loads such as operating costs, environmental footprints, etc. Amongst these operations, …
While electronic detonators are perfectly suited for controlled blasting in open pit mines, they also offer great flexibility to production blasts (Dent, 1994; Kay, 2000, Mckinstry et al. 2002; Chavez and Chantry, 2003, …
Blasting is regarded as a widespread rock fragmentation technique used in mining projects. Most of the blasting energy is squandered in generating unfavorable environmental effects like ground vibration, air-overpressure, flyrock and back-break [1,2,3,4,5,6,7,8].As stated by institute of markers of explosives (IME), flyrock is an …
Yang et al. based on the rock crushing mechanism and damage mechanics described the process of rock damage and fracture under blasting as two stages: the …
ROCK BLASTING FOR MINING. Prof. A. Balasubramanian. Centre for Advanced Studies in Earth Science. University of Mysore. Mysore-6. Objectives: You are all aware that Mining is a major econom ic ...
Request PDF | Optimized Burden-Spacing for Improvement of Rock Fragmentation by Blasting in Limestone Mines | Blasting with the aim to reduce …
Step 2: Planning. During the planning phase, mining professionals must determine blast hole pattern and detonation sequence. Both are optimized to break the rock efficiently and to minimize ground vibration and sound. …
The economic analysis of the use of explosives is an important part of blasting operations in mining and construction. Explosives are energy, and the efficient use of this energy is a major factor in keeping rock blasting costs under control. High-energy explosives enhance fragmentation, which ultimately produces a positive effect on production ...
Except for very deep-seated deposits, open cast mining method has been recognized as the safest and most productive mode for mining minerals. Ever growing demand in minerals and coal has compelled the mine operators to increase the size of mine, which has resulted in an increasing trend towards large capacity open cast …
Launching angle and launching velocity of flyrock projectile for each blast of all the limestone mines under the study with appropriate symbols are shown in Table 1, Table 2. The flyrock distances have been calculated using general trajectory formula ( Richards and Moore, 2004 ): (1) R fc = v 0 2 sin ( 2 θ 0) g.
Optimization of blasting design in open pit limestone mines with the aim of reducing ground vibration using robust techniques. Afsaneh Rezaeineshat, M. Monjezi, …
Massive Department National Institute of Health. Pillar Collapses in Coal for Occupational Safety Human Services, Assessing pillar Outreach collapse Seminar, and airblast and Health. hazards in underground stone mines. C, Rumbaugh, Meeting, November 9, 2021. Presented at the Mt. Pleasant 41st Intl. G.
process flow diagram for limestone processing operations 3 list of tables 6 6 table 1. gross energy to produce one ton of limestone products table 2. water consumption for limestone quarrying and processing table 3. lci inputs for limestone quarrying and processing table 4. lci outputs for limestone quarrying and processing table 5. other ...
This paper presents a case study of limestone mine where a controlled blasting was conducted near a green structure of wagon tippler (at 2 m) being constructed for foundation work of belt conveyor as the mine management wants to …
BASANTNAGAR LIMESTONE MINES. MINING PROCESS: It is fully mechanized opencast mine adopting top slicing method of mining, developing the benches by clearing overburden well in advance. 1) Drilling 2) Blasting 3) Leveling by Dozer 4) Handling of waste rock. 5) Lime stone Transportation 01. DRILLING.
Influence of front row burden on fragmentation, muckpile shape, excavator cycle time, and back break in surface limestone mines. Iranian Journal of Earth Sciences, 10(1), 1-10. Chouhan, L.S., & Raina, A.K. (2015a). Analysis of In-Flight Collision Process During V-Type Firing Pattern in Surface Blasting Using Simple Physics.
The whole process of making any type of lime all begins at the limestone quarry after careful surveys. Most limestone is extracted through blasting. Behind the rock face, holes are drilled to place the explosives. When detonated, the explosion dislodges each time up to 30,000 tonnes of stone.
حقوق النشر © 2024.Artom كل الحقوق محفوظة.خريطة الموقع