Ball Mill Design/Power Calculation
The basic parameters used in ball mill design (power calculations), rod mill or any tumbling mill sizing are; material to be ground, characteristics, Bond Work Index, …
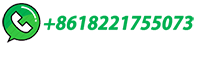
The basic parameters used in ball mill design (power calculations), rod mill or any tumbling mill sizing are; material to be ground, characteristics, Bond Work Index, …
Techno Designs is a ball mill manufacturer with an experience in designing, engineering, and manufacturing over 150 grinding mills. We deliver quality-approved batch type ball mills with sizes in the range of 1.5m x 2m and 3m x 7.5m and power ranging from 50 HP to over 1000HP. Our grinding mills have been tried and tested with a wide variety of ...
Ball mill In properly designed and operated overflow ball mills, the shell is protected by the ore and media charge; there should not be any direct media-to-liner impact. The hardest, most wear-resistant alloys can be used. Some ball mills are equipped with grate discharge systems. They require softer alloys, as it is difficult to ensure
The one of main problem in cement industry is the continouse abrasion in lining plates of cement mill as a result of impact, abrasive and erosion by steel balls grinding media inside cement mill.
Type CHRK is designed for primary autogenous grinding, where the large feed opening requires a hydrostatic trunnion shoe bearing. Small and batch grinding mills, with a diameter of 700 mm and more, are available. These mills are of a special design and described on special request by all Ball Mill Manufacturers.
Figure 5. High–low wave ball mill liner Materials The selection of the material of construction is a function of the application, abrasivity of ore, size of mill, corrosion environment, size of balls, mill speed, etc. liner design and material of construction are integral and cannot be chosen in isolation.
Ball Mill & Rod Mill Design. In all ore dressing and milling processes, including flotation, cyanidation, gravity concentration, and amalgamation, it is necessary to crush and grind, often with rob mill & ball mills, the ore in order to liberate the minerals. In the chemical and process industries, grinding is an important step in preparing raw ...
You also need a rod mill work index to design a ball mill operating on a coarse feed, above about 4 mm. Q1: You design for a typical percentage of critical speed, usually 75% of critical. Then you iterate the mill diameter using a Morrell C-model or equation to get the RPM that corresponds to 75% for that mill diameter.
The ball mill contains a hollow cylindrical shell that rotates about its axis. This cylinder is filled with balls that are made of stainless steel or rubber to the material contained in it. …
spacing and height of lifter bars, and to minimize liner/lifter and ball damage by avoiding. impact onto the mill shell. This paper presents a short review of mill liner design and its effects on ...
In this module, you will learn how to characterize the performance of ball mill circuits. Specifically, after completing this module, you will be able to: List and describe the four elements of the functional performance equation for ball mill circuits. Define and calculate the classification system efficiency of a ball mill circuit.
Optimal mill designs engineered by our team take into consideration service life; grind & power efficiency and ore characteristics, along with costumer circuit constraints both up and downstream of the mill lining. ... Our ball mill liners solutions can be fitted with MultoMet composite lifter bars, shell plates, and head plates. The manganese ...
Grinding in ball mills is an important technological process applied to reduce the. size of particles which may have different nature and a wide diversity of physical, mechanical and chemical ...
See more on 911metallurgist
WEBDefine and calculate the grinding efficiency of the ball mill in a ball mill circuit. Relate overall ball mill circuit output and circuit efficiency to specific design and operating …
The GrabCAD Library offers millions of free CAD designs, CAD files, and 3D models. Join the GrabCAD Community today to gain access and download! Learn about the GrabCAD Platform ... ball mill …
High Energy Ball Mill Emax. Sample volume up to 2 x 45 ml. Final fineness*: 0.08 µm. Highly effective size reduction mechanism. Water cooling permits continuous operation. Product details. Nanoscale Grinding.
Call us at 330.929.3333, contact us or click here to find a rep in your area. In discussions on high energy ball milling, the more generic term "ball mills" is often used in place of the terms "stirred ball mills" or "Attritors," …
Ball mill is a type of grinding equipment that uses the rotary cylinder to bring the grinding medium and materials to a certain height and make them squeeze, impact, and grind and peel each other to grind materials. Ball mill is the key equipment for crushing materials after they are crushed. It is widely used in cement, silicate products, new ...
There are numerous types of mill designs including autogenous, semi-autogenous, ball, rod and scrubber mills. This guide will refer to the two most common varieties: Semi-autogenous (SAG) and ball mills. ... Ball mills, conversely, contain grinding media up to 50mm in diameter, occupying between 25% - 40% of mill chamber volume. To …
Stirred mills have unique designs and operations, which provide higher grinding efficiency, lower energy consumption, and reduced media consumption compared to traditional tumbling mills. ... Ball mills have high energy requirements, and the efficiency of the size reduction is low, with a product finesse limit of 40–45 µm . Hence, there are ...
Ball mills are used primarily for single-stage fine grinding, regrinding, and as the second stage in two-stage grinding circuits. According to the need ball mill can be either for wet or dry designs. Ball mills have been designed in standard sizes of the final products between 0.074 mm and 0.4 mm in diameter.
Planetary Ball Mills: They are a form of vertical ball mills used for testing laboratories. They have smaller chamber balls and a limited capacity. It is only available in smaller sizes so as to ensure that it can be comfortably placed on tables or benches. Ball mill manufacturers of India are increasingly experimenting with the form, structure ...
The grinding tests were conducted in both vertical and horizontal orientations in the dry stirred ball mill with different stirrer velocities, media diameters and stirrer designs. The stress intensity model was used to compare the grinding performances while considering the orientation of the stirred mill (vertical/horizontal).
The balls to powder ratio (BPR) and powder type were investigated in relation to the particle size. The study showed that the combination of the BPR and powder type affects the particle size result. The optimum of BPR at 12 with the number of balls is 60 pieces, and the filling rate is 10.13%. The result shows that the horizontal ball mill able ...
ball mill chamber generally requires – depending on the desired size reduction – bigger media at the chamber inlet and ... the industry has developed so-called classifying liners in a variety of shapes and designs. The task of the liner is to influence the ball charge movement such that larger balls accumulate more towards the mill inlet ...
Stirred Mills – Ultrafine Grinding. In Mineral Processing Design and Operations (Second Edition), 2016. 10.2.4 Operation of Vertical Mills. Vertical stirred mills are usually charged with media occupying 80% of the mill volume which is in sharp contrast to tumbling mills that are seldom charged more than 40% of their volumes to allow space for the tumbling …
Ball mill (crusher machine) Mahmoud Ezzat ElNaggar. December 3rd, 2022. design for ball mill stone crusher. Download files. Like. Share. 517 Downloads 22 Likes 1 Comments.
You also need a rod mill work index to design a ball mill operating on a coarse feed, above about 4 mm. Q1: You design for a typical percentage of critical speed, usually …
Ball Mill Design Parameters. Size rated as diameter x length. Feed System. One hopper feed; Diameter 40 – 100 cm at 30 ° to 60 ° Top of feed hopper at least 1.5 meter above the center line of the mill.
partition device, support device, transmission part and feeding and discharging device of the ball. mill are designed. In this paper, the design method of three chamber ball mill is introduced ...
حقوق النشر © 2024.Artom كل الحقوق محفوظة.خريطة الموقع