Coated cutting tools and their applications | TJ Grinding
1. Hardness. Selecting a coating with high surface hardness will indefinitely increase tool life. Compared to the uncoated tool and coolant you typically can run coated tools at speeds two to three times higher. If you are looking for a coating that offers good adhesion, resistance to chipping, and a great level of toughness either go for ...
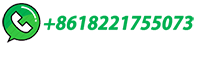