Cement Ball Mill | Cost Effective Cement …
AGICO cement ball mills have a wide range of models, with a maximum output of 130 tons per hour, which can meet the production needs of large, medium, and small cement manufacturers. Based on the grinding …
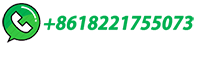