Vibration Feature Extraction and Analysis of Industrial Ball Mill …
The use of advanced technologies such as Micro-electromechanical system (MEMS) sensors and low power wireless communication hold a great promise for optimal performance of industrial wet ball mill. The direct translation of the natural phenomena of the batch mill in a lab setup to a continuous process mill in the industry is quite …
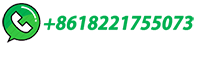