Solids | Choose the Right Grinding Mill
Dry grind mills also are used to make dispersion strengthened metal (DSM). In this process (known as mechanical alloying or cold welding) the grinding media break the metals and additives into small particles first, and then beat them together to form agglomerates. ... A ratio of feed size to desired particle size of greater than 100:1 …
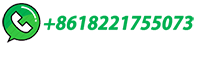