Grindability Studies of Mineral Materials of Different …
and iron ores samples were ground using a ball mill in different grinding conditions (dry and wet) and at different critical speed (R 45%, R 70% and R ... low density and soft materials than high density and hard materials. The relative increase in the fineness (D 80) for coal, dolomite, manganese ores and ... studied iron ore samples are given ...
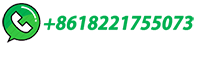