A comparative study on the effects of dry and wet grinding on mineral …
Chapman et al. (2013) compared the effects of using different circuits HPGR (dry) -rod mill (wet) and cone crusher (dry) -rod mill (wet) on the flotation of base metal sulfides. They indicated that apart from the grinding environment, HPGR could produce finer particles than a cone crusher. This difference was higher in the fully dry system.
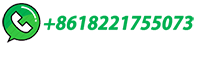