CN101455997A
The invention belongs to the field of ore and metallurgy, and in particular relates to a method for improving ore-dressing recovery rate of molybdenum. The method comprises: subjecting tailings obtained after gold separation by cyanation to preferential floatation of molybdenum directly, subjecting the tailings of the preferential floatation to scavenging …
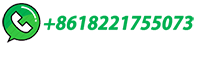