Effects of mill design and process parameters in milling dry extrudates
6.2.1. Effect of screen size. In both mills, with an increase in the screen diameter, particle size at the mill discharge increases. For the Comil, as shown previously, an increase in the screen diameter decreases the residence time in the mill, meaning fewer number of impeller passes (breaking action) on the material.
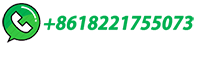