Raw materials used for Cement Production
The other important raw material for cement manufacture is clay. Clay is formed by the weathering of alkali and alkaline earth containing aluminum silicates and of their chemical conversion products, mainly feldspar and mica. The main component of clays is formed by hydrous aluminum silicates.
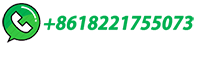