(PDF) Optimizing the control system of cement milling: Process …
Opti mizi ng the Co ntro l S yste m o f Cement Milling: Process Modeling and Controller Tuning Based on Loop Shaping Procedures 167 Brazilian Journal of Chemical Engineering Vol. 31, No. 01, pp ...
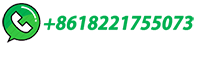