Analysis of vertical roller mill performance with
Abstract. The vertical roller mill (VRM) is commonly used for secondary and tertiary crushing processes in numerous industries. In this study, the discrete element …
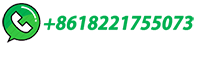
Abstract. The vertical roller mill (VRM) is commonly used for secondary and tertiary crushing processes in numerous industries. In this study, the discrete element …
Soft sensor enables computing parameters that can be physically impossible to measure. This work aims to develop a soft sensor for raw meal fineness in a vertical …
the production process also includes thyssenkrupp's latest-generation high-efficiency sepol® separator. For raw grinding the HDZX double cyclones are part of the technical …
Sensor Technology at the Vertical Raw Mill (VRM) 1. Optimization of the Grinding Process: Measurement at the VRM allows for precise regulation of the recirculation of dust-laden primary air. Accurate control optimizes the grinding process, resulting in finer grinding and improved quality of the end product. 2.
The fineness of raw materials used to be controlled at the level of several percents of 90 micron residue in the old wet process or others. As the burning method changed to SP and NSP, efforts were made to reduce the power consumption rate at the raw material process by increasing coarseness.
The grinding process in such mills occurs due to abrasion, respectively, in the process of work wear of the rubbing parts of the mill occurs. The work evaluated the performance of a mill with ...
process condition and taking corrective action in time. In this paper, the various conventional and modern control strategies to control the process variable available in …
Vertical roller mills (VRM) have become the standard for grinding raw materials in the cement manufacturing process. However, despite the fact that more than 10 years has passed since the ...
Vertical Roller Mill (VRM) is the most advanced technology in cement production procedure. Bashundhara Cement has adopted VRM from LOESCHE, Germany in both the factories to ensure the best quality. ... The rollers are driven by the friction between table & raw materials. The grinding process is done by exposing a bed of material to a pressure ...
A process simulator was used to study an industrial-scale vertical raw mill (VRM) with 65.4% energy efficiency. The paper proposes further a new model based on grid partitioning, sub-clustering, and fuzzy c-means, which incorporates genetic algorithms (GAs) and particle swarm optimizations (PSOs).
In this study, the analyses of energy and exergy were implemented for an industrial-scale vertical roller mill (VRM) of Kerman Momtazan Cement Company (KMCC) of Iran. The energy and exergy analyses demonstrated the first law efficiency of the VRM is 62.1%, while the second law efficiency of the VRM is 34.6%.
Unveiling the Vertical Roller Mill. In the ever-evolving world of industrial machinery, vertical roller mills (VRMs) have gained immense popularity for their efficiency and versatility. This powerful milling machine is used across various industries, including cement, mining, and chemicals, to grind raw materials and achieve finely ground products.
PROCESS TRAINING for operators of Vertical RAW Mills. Heating of mill and grinding plant. In fact there are three processes going on in the MPS …
Vertical roller mills (VRM) have become the standard for grinding raw materials in the cement manufacturing process. However, despite the fact that more than 10 years has passed since the installation of the first VRM for clinker grinding was almost completed, many cement producers are still favouring ball mills for cement production …
Vertical roller mills (VRM) have been used extensively for comminuting both cement raw materials and minerals like limestone, clinker, phosphate, manganese, magnesite, feldspar and titanium. These mills combine crushing, grinding, classification and drying operations in one unit and have advantages over conventional machines and …
For new cement plants, our process expertise and product portfolio deliver plants with the minimum environmental footprint. And what is good for the environment can also be good for profitability, as energy efficiency coincides with minimising the cost of fuel and power. ... Superior mill liners, service and support combine to improve mine's ...
UBE Mills are capable to grind and dries all the types of coal. We offers the coal mill to suited for various installation types, whether inert or non-inert. Our technology and experience to offer reliable solution and ensures the …
This can be counted yearly as over 6% of global energy consumption. More than 60% of this tremendous energy has been used in the comminution units (crushers and mills) to reduce the size of raw materials and clinker 1–3. In the mid-1990s, the vertical roller mill (VRM) was introduced to the cement industry to reduce this energy usage.
A vertical roller mill (VRM) is a grinding equipment used for the size reduction of minerals, cement, and ceramics. ... size reduction of raw materials is an energy-intensive operation. A vertical roller mill is a grinding equipment for many industries such as minerals, cement, and ceramics. ... West MP (1991) Process …
explains complete process of identifying possible causes and final root causes, finding possible solutions and implementing them in order to increase the output of vertical roller mill. This study can benefit the organizations using VRM and are not able to utilize its full productivity due to some bottlenecks or constraints. 1. Introduction
A VRM offers several possibilities to control the grinding process. Altogether there are six online controls (marked with * in Fig. 1), which can be adjusted while the mill is running.Furthermore, roller geometry and dam ring height are important design features in a Loesche mill, which can be adapted to the grinding task.
vrm raw mill process Design of intelligent control system for Vertical Roller Mill. WebJul 1, 2011 Vertical roller mill (VRM) is a large-scale grinding equipment, which is used to grind raw materials from block/granule into powder. ... WebMay 9, 2022 The raw vertical roller mill has four rollers, 3000 KW main drive, 4.8 m table diameter, 2.16 m ...
The raw mill is either a Ball mill with two chambers or Vertical roller mill with inbuilt classifier. The hot gases from the pre heater enter the mill and are used for drying …
cement ball mill. Application: limestone, clay, coal, feldspar, calcite, talc, iron ore, copper, phosphate, graphite, quartz, slag. Capacity: 0.65-615T/H. The cement ball mill usually can be applied to raw meal grinding or cement grinding. Besides, the cement ball mill also can be used for metallurgical, chemical, electric power, other mining ...
re VRM vs Ball Mill for Cement Grinding. Specific power consumption- high for ball mill and Low for VRM. Maintenance costs- high for VRM and low for Ball mill. Process control/process technology- ball is operation friendlt and simple in operation but VRM requires some PID or control technology. Plant/system auxiliaries- less auxillaries …
Vertical raw mill pradeep kumar - Download as a PDF or view online for free. ... The grinding process starts with the preparation of the so- called grinding bed, where the coarse material is crushed. ... Exception handling • 2.1 vertical roller mill vibration is too large: (1) Feed uneven, when the mixture into the vertical roller mill over ...
In the study the advantages of vertical roller mill are discussed over ball mills. VRM construction, its process and parameters which affects the performance and productivity of vertical roller mill are discussed. ... In the wet/semi-dry process, the raw materials are produced by mixing limestone and water (called slurry) and blended with …
Used a VRM (Loesche mill) with 160 t/h to grind the clinker, fed into the mill during the grinding process (%90 passing 32 mm). Fig. 3 shows the grinding circuit for VRMs. The Loesche VRMs at the Ilam cement plant are equipped with four rollers, two of which are master rollers and small support rollers performing grinding and layering of the ...
The power ingesting of a grinding process is 50-60% in the cement production power consumption. The Vertical Roller Mill (VRM) reduces the power consumption for cement grinding approximately 30-40 ...
How to operate a raw material (coal, limestone, rock) vertical roller mill-a comprehensive guide to… Brief description of the process flow of raw material vertical mill system 18 min read · Dec ...
حقوق النشر © 2024.Artom كل الحقوق محفوظة.خريطة الموقع