Influence of dry grinding on physicochemical …
The dry grinding was performed in a vibrating ball mill at various grinding times (5-150 min) by keeping the grinding parameters constant such as the number of ball, ball size, the amount of talc ...
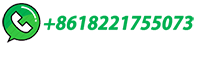
The dry grinding was performed in a vibrating ball mill at various grinding times (5-150 min) by keeping the grinding parameters constant such as the number of ball, ball size, the amount of talc ...
talc and the non-polar naphthalene molecules in an aqueous environment (S ener and O¨zyılmaz, 2010). In contrast, the hydrophilicity of talc increased by grinding and disintegration of the talc structure (Terada and Yonemochi, 2004). The aim of the present paper was to compare the effects of a mechanical grinding and sonication process
Talc: dry grinding. As reported in Zbik and Smart (2002) and confirmed here, short grinding times in the ring mill had a significant effect on the talc platelet diameter, breaking platelets and lowering the aspect ratio. ... (51.19 % and 10.36 µm 2, respectively), and this can be attributed to finer particles and a higher amount of Fe (1.08 % ...
The optimum feed rate, classifier rotational speed, and grinding pressure for talc were 12 kg/h, 7000 rpm, and 6 bar, respectively. Ground talc exhibited mechanochemical effect where the degree of crystallinity ranged from 26.5% to 85.3%. Talc ground at 4 kg/h, 13,000 rpm, and 6 bar exhibited massive mechanochemical effect …
The grinding of talc was carried out by using two different sizes of balls (4 mm and 10 mm), at 60 % solid content in slur-ry, 175 r.p.m, and different grinding times. Figure 4 shows the results of grinding using (a) (3.6 Kg) 4 mm & (b) (3.6 Kg) 10 mm alumina balls. It has been found out that the efficiency of grinding using 10 mm ball size is ...
Introduction of Talc Grinding Mill. Clirik HGM Series talc grinding mill is widely used for micron powder producing. The output size can reach 3000 mesh. It is suitable to grind the material with middle and low hardness, moisture below 6%, and the material should be non-explosive and non-flammable, such as: calcite, chalk, limestone, dolomite ...
Process: (1) First, crush and grind talc to separate talc from the associated minerals; (2) Then, send talc to a ball mill for wet grinding. 90%-95% of talc has a particle size less than 0.074mm and is sent to a …
Fig. 1 shows SEM images of pristine and ground talc samples, as well as their alkali-activated counterparts obtained after 24 h treatment with NaOH solution. The untreated talc powder consisted of stacks of thin, sharp-edged plates (Fig. 1 a), and alkali treatment did not affect its morphology in any noticeable way (Fig. 1 b).Upon 10 min of …
Talc grinding in an opposed air jet mill: start-up, product quality and production rate optimization L Godet-morand, Alain Chamayou, John A. Dodds ... 70 g/min (about 4 min) than for 51 g/min (about 5 min) or 22 g/min (about 7 min). In practice, 15 min were allowed even though for the lowest feed rates, only 7 min were
Abstract Talc, as an industrial mineral, is usually used at fine and ultrafine sizes in different applications. However, reaching the ultrafine sizes depends simultaneously on grinding conditions and the characteristics of the mineral to be ground. In this paper, the effect of talc hydrophobicity and grinding conditions in terms of grinding balls size, mill …
Keywords: Talc; Grinding; Shape characteristics; Surface roughness; Wettability; Floatability 1. Introduction known that the character of the material and the type of mill employed determine the shape of the particles produced. ... New York, 1964, pp. 1 – 51. cLV Liquid – vapor surface tension, mN/m [15] M.C. Williams, D.W. Fuerstenau, A ...
The grinding produces a progressive increase of the accessible sites for NI-I4+ and Naions. Okuda et al. (1969) reported that the CEC of talc increased from 0.4 meq/100 g to 1.5 meq/100 g when the surface is incremented up to 20 m2/g by grinding; in this study, the mineral remained unchanged with respect to its crystallinity (i.e. no ...
In this study, the effect of sodium dodecyl sulfonate (SDS), as a well-known flotation collector, on talc grinding was investigated using a statistical design in terms of solids%, pH, grinding time, and SDS …
Talc is a magnesium silicate clay mineral and when present in molybdenite concentrate, contributes to the acid-insoluble content. Talc has a laminar structure as shown in Fig. 4.As can be seen, talc is a tri-layered hydrated magnesium silicate with a chemical formula of 3MgO·4SiO 2 ·H 2 O or Mg 3 (Si 2 O 5) 2 (OH) 2 (Xu et al., 2018, …
This research brief identifies how talc moves around the world, from mines to Johnson & Johnson's production hubs, to distributors in the global South. Three mines (in China, India, and Brazil) provide the talc used by J&J worldwide. This brief identifies the flow of raw talc from the mines to four mills that grind it, and from there, to J&J ...
Talc grinding in an opposed air jet mill: start-up, product quality and production rate optimization. Laurence Godet-Morand, A. Chamayou, J. Dodds. …
In this study, shape characteristics of talc particles produced by ball, rod and autogenous mills were investigated using Scanning Electron Microscope (SEM) and expressed by the shape descriptors ...
Abstract. This manuscript aimed to examine the impact of operating parameters on the wet grinding of talc in a vertical-type stirred media mill. Within the …
The optimum feed rate, classifier rotational speed, and grinding pressure for talc were 12 kg/h, 7000 rpm, and 6 bar, respectively. Ground talc exhibited mechanochemical effect where the degree of ...
Twarda 51/55, 00-818 Warsaw, Poland Received 23 October 1995; revised 21 February 1997; accepted 21 February 1997 Abstract The effect of dry grinding on the structure, particle size and shape of talc from Puebla de Lillo (Le6n, Spain), was studied by means of nitrogen adsorption, XRD, DTA-TG and by SEM-EDS methods.
MAS NMR and EPR study of structural changes in talc and montmorillonite induced by grinding | Clay Minerals | Cambridge Core. Home. > Journals. > Clay …
Enter the email address you signed up with and we'll email you a reset link.
United Mineral Group Of Companies is the main source of minerals in the region working from last 16 years having expertise in extraction, processing and trading of talc minerals. UMTC is an independent company operating in trading, wholesale and supply of natural mines and talc at a European level, with a special focus on the Turkish and ...
The flotation feed preparation significantly affects the concentrate quality. In this study, the preparation of talc flotation feed by grinding was investigated in the …
Nissan 300 tons talc grinding . China Heavy Industry is an import-export joint-stock company that specializes in the production of large and medium-sized broken, sand-making and milling equipments, research, production, and sales.It is committed to providing customers with integrated solutions.More than 10 series and dozens of specifications of …
Talc ground at 4 kg/h, 13,000 rpm, and 6 bar exhibited massive mechanochemical effect where the degree of crystallinity was 27.6%. The crystallite size …
It was found that grinding caused an increase in the surface area of the natural talc from 3 m2g-1 to 110 m2g-1. A decrease of particle size after sample grinding was observed by SEM. The increase of structure disorder of the ground sample and the crystallite size reduction from 40 to 10 nm were determined from the XRD results.
Grinding: Grind the screened limestone into powder to expand its application range. Commonly used grinding equipment include ball mills, vertical mills, Raymond mills, etc. ... Talc Ultrafine Grinding Mill. Capacity: 0.2-45 t/h Max feeding size: 20 mm Discharge fineness: 150-3000 mesh
CHINA SUPER MICRON TALC GRINDING MILL PROJECT 14:51. Equipment model and number: 2 HC1000. Processing material: Talc. Finished product fineness: 325 mesh D99. Equipment output: 4.5-5t/h A large talc company in Guilin is one of the largest talc companies in China. The preparation of pharmaceutical-grade …
The fine grinding testwork was carried out with an Alpine 100 AFG fluidized bed jet mill (hereafter, referred to as jet mill) equipped with a 50 mm ATP-forced vortex classifier (hereafter, referred to as classifier) as shown in Fig. 1. Fig. 1 also shows other unit operations attached to the jet mill, such as an air cyclone and a bag filter Table 1 shows …
حقوق النشر © 2024.Artom كل الحقوق محفوظة.خريطة الموقع