Chapter 20 Modelling of Mills and Milling Circuits
Vertical spindle mills. A mathematical model for a spindle mill with a built-in cone classifier has been proposed by Austin et al. [28]. Because the rotating balls in the mill cause intensive mixing, the mill can be treated as fully mixed. The mill–classifier circuit is built up according to Fig. 4. The first classification action arises from ...
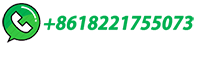