Removal of sodium oleate from synthetic …
Removal of sodium oleate from synthetic manganese leaching solution by coagulation-dissolved air flotation. JianrongXueab, HongZhongb, ShuaiWangb. Show …
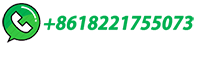
Removal of sodium oleate from synthetic manganese leaching solution by coagulation-dissolved air flotation. JianrongXueab, HongZhongb, ShuaiWangb. Show …
Dodecylamine is one of the most commonly used amine collectors for the reverse flotation of magnesite ore. Through a combination of experimental research and computational simulation, the effect of n-octanol on the removal of impurities by the reverse flotation of magnesite ore was studied.The test results show that when the dosage of dodecylamine …
In this operation the ore is ground to approximately minus 24 mesh and the impurities removed by froth flotation with the usual reagents for non-metallics. Salt Flotation. Flotation has been successfully used in Canada for removal of impurities from sodium chloride.
Vale is the largest iron ore producer in the world. Since the 1970s, Vale has been using reverse cationic flotation to remove siliceous impurities from its iron ores. Whilst this flotation process has operated effectively for many years, it suffers from the problems of high reagent costs and high metal loss.In 2010, CSIRO investigated the use ...
The FLOTATION PROCESS is one of the commonest methods of extracting the valuable minerals from certain classes of ores, and it is generally more efficient as regards the recovery of the minerals than any other process applicable to the treatment of similar types of ores. The metallic contents of the minerals are recovered from the …
The impurities accumulating in the process may stem from raw water, originate from flotation reagents, or dissolve from the ore to the process water . …
Froth flotation is a physicochemical process that is used to separate fine mineral particles from aqueous suspensions by selective attachment of some types of minerals to air bubbles. Froth flotation is the most important mineral processing technology for the production of valuable mineral concentrates from which metals and minerals are …
Zhang et al. [26] performed hydroxide precipitation at 60 °C with NaOH solutions for removal and recovery of manganese(II) from synthetic laterite waste solution containing 2 g/L Mn 2+, 15 g/L Mg 2+ and 0.5 g/L Ca 2+ (Table 2).At pH 8.2, 71% precipitation of Mn 2+ occurred along with 5% Mg 2+ co-precipitation. At pH >9, the …
Through a combination of experimental research and computational simulation, the effect of n-octanol on the removal of impurities by the reverse flotation of magnesite ore was studied. The test results show that when the dosage of dodecylamine was 60 mg/L, the flotation rates of magnesite and dolomite were 59.53% and 58.02%, …
Froth flotation is an efficient method to remove impurities from iron ore when the valuable and impurity minerals are liberated. The separation is achieved by exploiting differences in the physicochemical properties of the iron and impurity minerals. ... Kaolinite removal in iron ore flotation is complex in that it involves interactions between ...
Research regarding iron ore flotation began in 1931, demonstrating that reverse. cationic flotation is a very efficient method for beneficiating oxidised iron ores. This method can also. be ...
Beneficiation of low-grade phosphate deposits through direct froth flotation has captured more attention to satisfy the future needs of phosphorous industry. This is owing to the excessive consumption of the global reserves of high-grade phosphate deposits. Phosphate flotation using mixed collectors has been proved to give greater selectivity and high …
Removal of phosphate impurities is a prerequisite for using phosphate ores in different applications. The flotation process is one of the most promising processes that have been used to improve ...
ores) is partially purified using another important technique which is called froth flotation and it is the topic of our discussion as well. Froth flotation is such a cheapest technique of metallurgy which is widely used all over the world for low grade sulfide ore concentration to remove the impurities.[3]
Indian low grade iron ores mostly contain quartz, gibbsite, and clay as the major impurities.Depending upon the ore characteristics, in many instances froth flotation has to be used to recover the hematite and other iron oxides from the ground ores. In this context, the difference in silica and alumina content in low grade iron ores is brought to …
However, it requires the use of starch as iron depressant. 3) A combined process of magnetic separation and reverse flotation is effective for removal of silica and alumina from Sanje ore. As proposed circuit, iron …
Applications of SX for manganese separation/removal. Manganese is closely associated with zinc ores and nickel–cobalt laterite ores and leached together with these metals. Solvent extraction plays an important role in separation of these metal values from manganese, in which manganese is left as an impurity in the raffinate.
A systematic study of the design and operating condition has been made for key performance metrics such as removal of toxic heavy metal from sulfide ores, recovery of KMnO4 from sludge containing ...
At a yield of 71.22%, a concentrate with a grade of 97.16% and impurity contents of 0.18% SiO2, 0.60% CaO and 0.49% Fe2O3 was obtained by 3 stages of reverse flotation using the KDL collector. The floated material was rejected as tailings, and the fraction that did not float offered the anionic reverse flotation.
FLOTATION Section A-Research paper 17 Eur. Chem. Bull. 2023, 12(5), 17-29 Recovery of Manganese Ore using pine oil as frother in Froth Flotation K. Ganapati1, Dr. Ch. Asha …
Dodecylamine is one of the most commonly used amine collectors for the reverse flotation of magnesite ore. Through a combination of experimental research and …
Froth flotation has been established as an efficient method to remove impurities from iron ore in half a century's practice around the world. Reverse cationic flotation is currently the most ...
The literature on the processing of phosphate rocks by flotation is critically reviewed. Commonly used collectors, depressants, auxiliary reagents, and their mixtures in the flotation of the phosphate ores were tabulated. The advantages and disadvantages of the reagent type and structure (e.g., ionic and nonionic) on flotation were criticized.
Phosphate rock contains various gangue minerals including silicates and carbonates which need to be reduced in content in order to meet the requirements of the phosphate industry. Froth flotation has become an integral part of phosphate concentration process. In this study, double reverse flotation was applied to recover apatite from …
a cheapest technique of metallurgy which is widely used all over the world for low grade sulfide ore concentration to remove the impurities.[3] . Flotation is …
Manganese Ore Concentration by Flotation. The slime fraction of the ore overflowed by the hydraulic classifier and by the rod-mill spiral classifier is thickened in a Spiral Rake Tray Thickener for …
Current study investigates the SO2 leaching of low-grade ferruginous manganese ores to selectively recover manganese as MnSO4 and subsequently produce battery grade electrolytic manganese dioxide (EMD) from the purified MnSO4. The effect of leaching process parameters such as leaching duration, temperature, and the SO2 flow …
Increasing demand for manganese and rapid depletion of high-grade manganese ores grow attention to other resources. However, environmental impacts and techno-economic issues are the main challenges regarding manganese extraction from low-grade ores. This study investigated the environmental impacts of manganese recovery …
The addition of sodium silicate enhanced the flotation efficiency through: 1) the removal of impurity minerals and calcium-bearing precipitates from quartz surfaces by dispersion, 2) drier and ...
The removal of impurities from MG-Si by hydrometallurgical processes depends on the sensitivities of the silicon substrate and the exposure of the impurities to the acid etchants. Thus, intensive measures, such as introducing external fields (e.g., ultraviolet radiation, ultrasonic field, and oxygen pressure leaching treatment) or …
حقوق النشر © 2024.Artom كل الحقوق محفوظة.خريطة الموقع