Multiphase flow simulation of a simplified coal pulveriser
It will be applied for 500MW coal-fired power plant capacity operated by South Korea N. Power Co., Ltd. The DSI process is adapted between a preheater and an EP(Electric Precipitation) process in ...
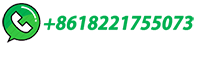