Cement Manufacturing Process – INFINITY FOR …
CLINKER COOLERS. In cement manufacturing, formation of clinker nodules occurs at the entrance to the hottest part of the kiln with a material temperature …
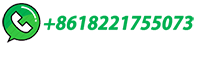
CLINKER COOLERS. In cement manufacturing, formation of clinker nodules occurs at the entrance to the hottest part of the kiln with a material temperature …
Cement Plant Process Equipment Clinker Grinding Unit Manufacturers. ... manufacturing process of these bearings requires the usage of high-end current technology. The common form of motions that are acknowledged by the bearings are hinge motion (e.g. knee, elbow and door), spherical rotation (e.g. socket joint and ball), linear …
Stage of Cement Manufacture. There are six main stages of the cement manufacturing process. Stage 1: Raw Material Extraction/Quarry The raw cement ingredients needed for cement production are limestone (calcium), sand and clay (silicon, aluminum, iron), shale, fly ash, mill scale, and bauxite. The ore rocks are quarried and crushed into smaller …
The clinker calcination is an important energy consumption process unit in the cement clinker manufacturing process, including rotary kiln, kiln hood and some auxiliary equipment. In this process unit, the materials, coming from the preheating & decomposition process unit, complete the heat exchange with high temperature reverse …
Use the form below to get in touch! The message minimum length requires 30 characters. With more information, we can provide you a faster quotation. AGICO cement machinery offers rotary kilns, cement mills, crushers, and many other cement manufacturing equipment for your cement business.
Because raw coal is still used in cement manufacturing, equipment that can grind coal onsite is necessary for most cement plants. As with the actual milling of cement, manufacturing equipment used to break down the coal requires mechanisms with airlock capabilities. These must be able to handle capacities from 10-100 tons hourly.
6 steps of the cement manufacturing process. When we talked about the manufacturing of cement, anyone who knows the cement manufacturing process slightly will mention "two grinding and …
As Clinkerization process is an endothermic (heat absorbing) process it requires burning of Suitable fuel. Remember almost 40 % of the total cost spent for manufacturing cement is for fuel and power. The specific heat consumption of modern plant ranges 690 to 800 Kcal/kg clinkers.
January 16, 2023. By. admin. Dr SB Hegde, Professor, Jain University, Bangalore, talks about pyroprocessing and the role of preheater, rotary kiln and clinker cooler in the cement manufacturing process. In the concluding part of the two-part series, we will learn more about the various factors aiding pyroprocessing. False Air in Pyro Processing.
In cement manufacturing, formation of clinker nodules occurs at the entrance to the hottest part of the kiln with a material temperature of around 1280°C. The clinker is preferably in the form of 10-mm to 25-mm size nodules that exit from the front end of the kiln into the cooler. ... Like other processing equipment, clinker coolers have ...
Clinker production can be divided into preheating and pre-calcining, clinker sintering, and clinker cooling three stages. Cyclone preheater, cement kiln, and clinker cooler are …
2. The limestone is combined with clay, iron ore and sand. It is then ground in a crusher and fed into. 3. Next, the fine powder is heated as it passes through the Pre-Heater Tower into a large kiln. In the kiln, the powder is heated to 1500oC. This creates a new product, called clinker, which resembles pellets about the size of marbles.
In cement manufacturing, formation of clinker nodules occurs at the entrance to the hottest part of the kiln with a material temperature of around 1280°C. The clinker is …
The clinker manufacturing process starts with the extraction of the raw meal from the homogenization silo to insure that the raw meal is stable and homogenized in order to produce consistent clinker quality. The preheating of the material takes place in pre-heater cyclones fitted with a pre-calciner fired with petroleum, natural gas or coal ...
10.3.3 Cement manufacturing. Cement manufacturing has several opportunities for WHR, specifically in the process step where the clinker material is produced. For clinker production, a mixture of clay, limestone, and sand is heated to temperatures near 1500°C. The kiln and clinker cooler have hot exhaust streams where waste heat could be …
In portland cement manufacturing, the raw materials are changed to clinker in the burning operation. Generally the rotary kiln is used for this purpose and involves many processes including pelletizing …
The cement industry is undeniably critical for the global economy. However, they are also the largest energy consumers in the world. The clinker manufacturing process causes gaseous emissions like nitrogen oxides, sulfur dioxide, carbon dioxide and particulate matter. There is scope for various technologies to be used in the cement …
Cement Equipment Supplier. AGICO Cement is located in Henan, China. It was founded in 1997 with a registered capital of 81.34 million yuan. It covers an area of 660000m 2 which includes a construction area of 30000 m 2. In 2004, AGICO passed the ISO9001 certification and enjoyed the self-management right of import and export.
Cement plants have used new grinding equipment, dry-process instead of the wet-process kiln, modern clinker kilns, and multi-stage preheaters that can save energy [1]. The use of blends with renewable fuel and fossil fuel [ 2 ] or the use of solar calcination reactors [ 3 ] can reduce emissions and save energy in cement manufacturing.
Explore the significance of clinker grinding in cement manufacturing, from particle size reduction to improved reactivity and quality control. Learn how this integral …
The manufacturing of clinkers is the first step in the cement production process. The clinker manufacturing process comprises three main components: crusher, roller mill, and rotary kiln.
With an unrivaled global network of operating companies and competent partners, the name Schenck Process is synonymous throughout the world with process expertise and well-engineered measuring technology for weighing, feeding, conveying, automation and air filtration. Schenck Process provides cement processing equipment.
Clinker grinding plants and cement plants hold significant significance within the cement manufacturing sector, as they are pivotal in generating essential raw materials required for the diverse…
Cement manufacturing is an energy intensive process. About 80% of the total energy required in cement manufacturing is consumed in the thermal conversion of raw feed into clinker. Typically, a long dry process kiln …
The final manufacturing stage at a cement plant is the grinding of cement clinker from the kiln, mixed with 4-5% gypsum and possible additives, into the final product, cement . In a modern cement plant the total consumption of electrical energy is about 100 kWh/t . The cement grinding process accounts for approx. 40% if this energy consumption.
People who know a little about the cement industry know that rotary kiln is the important cement equipment for processing cement clinker from raw materials. It can be divided into dry process cement rotary kiln and wet process cement rotary kiln, mainly composed of kiln cylinder, kiln head, drive device, support device, sealing device, fueling system, …
Industries. Infrastructure. Cement. Concrete end-to-end solutions you can count on. Delivering truly sustainable cement production requires a fully integrated approach that …
December 26, 2023. equipment. As we all know, the dry-process cement production line is commonly used in the cement industry. The new type of dry-process cement production process includes four main sections: Pre-homogenization of raw materials, homogenization of raw materials, clinker firing, cement grinding, etc.
Cement Mill. A cement mill is just a general term for clinker grinding mill. It is a kind of grinding equipment that used to grind the calcined cement clinker then make them reach the particle fineness requirement of the finished cement product. It is the core equipment of the last step in the cement production process.
The manufacture procedures of Portland cement is described below. Mixing of raw material. Burning. Grinding. Storage and packaging. 1. Mixing of raw material. The major raw materials used in the manufacture of cement are Calcium, Silicon, Iron and Aluminum. These minerals are used in different form as per the availability of the minerals.
حقوق النشر © 2024.Artom كل الحقوق محفوظة.خريطة الموقع