Iron Ore Beneficiation | ST Equipment & Technology (STET)
The STET dry electrostatic fine iron ore separation process offers many advantages over traditional wet processing methods, such as magnetics or flotation, including: No water consumption. The elimination of water also eliminates pumping, thickening, and drying, as well as any costs and risks associated with water treatment and disposal. ...
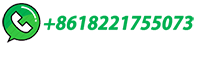