AUTOMATION AND OPTIMIZATION OF COAL GRINDING …
grinding 1 ton of coal (by 5 to 50 % depending on the type of the . mill) as well as increase of grinding capacity of the mill. Key words: coal grinding, ball mill, optimization, …
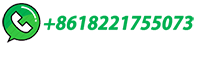
grinding 1 ton of coal (by 5 to 50 % depending on the type of the . mill) as well as increase of grinding capacity of the mill. Key words: coal grinding, ball mill, optimization, …
The ball mill is so common that it is utilized for primary, secondary, and tertiary grinding and regrinding in industries including mineral, cement, and coal; in dry or wet grinding processes; and ...
Attrition mill operating characteristics. L. Y. Sadler D. A. Stanley D. Brooks. Engineering, Materials Science. 1975. 39. Semantic Scholar extracted view of "Effect of operating parameters in stirred ball mill grinding of coal" by M. Mankosa et al.
A coal ball mill is a type of ball mill used to grind and blend materials for use in mineral dressing processes, paints, pyrotechnics, ceramics. It works on the principle of impact and attrition: size reduction is done by impact as the balls drop from near the top of the shell. ... Ball mill grinding media. Vertical roller mill grinding roller ...
1.. Case descriptionA Brazilian power plant consumes mineral coal with high ash contents to feed four turbines to generate 450 MW.Four ball mills, 4.2 m in diameter, are fed with crushed coal with maximum size of 25 mm and up to 20% humidity, to deliver the material ground to sizes less than 0.075 μm.Each ball mill is fed at a rate of 70 t/h …
If a ball mill uses little or no water during grinding, it is a 'dry' mill. If a ball mill uses water during grinding, it is a 'wet' mill. A typical ball mill will have a drum length that is 1 or 1.5 times the drum diameter. Ball mills with a drum length to diameter ratio greater than 1.5 are referred to as tube mills. Ball mills may be ...
The objective of this study is to investigate the effect of ball size on grinding kinetics in a pilot scale ball mill. Six different ball media gradings were tested. Comparative tests were conducted in batch ball mill having 1.2m diameter and 0.6m length at constant operating condition of mill such as media mass, mill speed and input specific ...
outlast several sets of grinding parts. Magotteaux Through a strategic alliance, B&W provides its advanced coal pulverizer wear parts from Magotteaux®, a leading supplier of high wear, severe duty castings and differentiated wear solutions. B&W's pulverizer tires, grinding segments, grinding rings, balls and other wear components are
The present work discusses a systematic approach to model grinding parameters of coal in a ball mill. A three level Box–Behnken design combined with response surface methodology using second order model was applied to the experiments done according to the model requirement.
Firstly, the conventional ball mill parameters such as mill speed (% of critical speed), material filling ratio (Jb), ball filling ratio (fc), ball size distribution (10-20-30-40 mm, %), grinding ...
Ball Mill Inspection Procedure - Free download as PDF File (.pdf), Text File (.txt) or view presentation slides online. "Doctor" is required for: 1) implementation of "Health checks" I Regular action 2) urgent …
This document provides guidance on ball mill grinding processes. It covers topics such as ball mill design including length to diameter ratios, percent loading, critical speed, and internals evaluation. Methods for assessing ball charge, wear rates, and liner management are described. Empirical relationships for power draw and grinding laws are presented. …
For a ball mill grinding OPC to a fineness of 3200 to 3600 cm2/g (Blaine) the cost of wear parts (ball, liners and mill internals) is typically 0.15-0.20 EUR per ton of cement. For an OK mill grinding a similar product, the cost of wear parts depends on the maintenance procedures, i.e. whether hardfacing is applied.
PDF | The paper presents an overview of the current methodology and practice in modeling and control of the grinding process in industrial ball mills.... | Find, read and cite all the...
The JOYAL Ф2700×3600 Ball mills are commonly used as secondary grinding equipment after crushing, and are used for various types of ore and similar materials, for either wet or dry grinding. They are mostly used in ferrous/non-ferrous metal mines, for building materials, chemical applications, el...
Two mill systems are employed for most coal grinding applications in the cement industry. These are, on the one hand, vertical roller mills that have achieved a share of almost 90 …
Request PDF | On May 1, 2014, M.M. Bwalya and others published Exploring ball size distribution in coal grinding mills | Find, read and cite all the research you need on ResearchGate
Ball mills are among the most variable and effective tools when it comes to size reduction of hard, brittle or fibrous materials. The variety of grinding modes, usable volumes and available grinding tool materials make ball mills the perfect match for a vast range of applications. Cooling, heating & cryogenic grinding.
The mineral processing industry has seen an increased use of vertical stirred mills, owing to the ineficiency of ball mills for fine grind applications. The difficulty encountered in …
The size of 30 mm was optimum for raw materials of −0.45 + 0.15 mm and −0.15 mm. The optimal ball size distribution was 12 mm (40%), 20 mm (40%), 32 mm (10%), and 40 mm (10%) for dry fine-grinding of calcite ore. Finer ball loads were unable to break coarser particles nipped in the feed.
• Ball mill specific grinding rate • Ball mill grinding efficiency The circuit output is defined as the production rate of fines by the circuit. It is calculated from three values: 1. The dry ore feed rate to the circuit (t/h). 2. The % fines in the circuit feed. 3. The % fines in the circuit product. Use this equation to solve for circuit ...
High degree of automation. Excellent material quality. Feeding size: ≤25mm. Capacity: 6.6-105t/h. Applicable materials: Coal, lignite, gangue and other materials. Get Price Now. Coal water slurry ball mill (CWS ball mill) is the key equipment for coal water slurry fuel production, which is commonly used in coal water slurry power plant.
The mineral processing industry has seen an increased use of vertical stirred mills, owing to the ineficiency of ball mills for fine grind applications. The difficulty encountered in fine grinding is the increased resistance to comminute …
A conventional grinding circuit consisting of one open-loop rod mill and one closed-loop ball mill is essentially a two-input×two-output system, assuming that the classifier pump box level is ...
Curves of mill productivity, power consumed, specific surface of coal dust in terms of the relative rotational speed of the ball drum mill Composition of the balls loading the mill with a standard ...
coal ball mill construction pdf – Grinding Mill China. Construction Design Of Ball Mill Pdf | Process Crusher, Mining … Construction Design Of Ball Mill Pdf 3 Views. … hammer mill free construction drawings and design pdf » More detailed! ball mill pdf. Application The ball mill is a key equipment for regrinding. It is widely used for ...
The energy con sumption for spherical balls was 3.6 Kw after grinding for 420 minutes, producing a 45µm. residue of 4.37% whilst that of cylpebs was 2.6kW after grinding for 295 minutes producin ...
Wet and dry grinding of coal in a laboratory-scale ball mill: Particle-size distributions | Semantic Scholar. DOI: 10.1016/j.powtec.2019.09.062. Corpus ID: 208764858.
Abstract: The ball mill is a rotating cylindrical vessel with grinding media inside, which is respon-sible for breaking the ore particles. Grinding media play an important role in the …
Grinding in ball mills is an important technological process applied to reduce the size of particles which may have different nature and a wide diversity of physical, mechanical …
حقوق النشر © 2024.Artom كل الحقوق محفوظة.خريطة الموقع