Development of a Novel Grinding Process to Iron Ore
Keywords Pelletizing .Agglomeration .HPGR .Milling 1 Introduction Modern iron ore pelletizing process operations may be divid-ed into two main process sections: feedstock preparation and agglomeration processes. In most plants, the required particle size distribution (PSD) is obtained through the wet ball mill circuit.
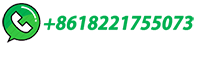