Nickel Ore Dispersion Evaluation and Consequences in Flotation …
Nickel ore dispersion before flotation using different reagents was investigated on a bench scale to improve metallurgical recovery and selectivity. The nickel ore had a content of 0.8 pct nickel and 14.5 pct MgO. A positive linear correlation between MgO and Ni was found. Carboxy methyl cellulose, both pure and combined with …
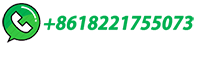