8 Tips For Cement Plant Design | Cement Manufacturing Process
The design of the cement grinding system is also focused on "energy saving", because the cement grinding part accounts for about 45% of the electricity consumption in the cement plant. There are many cement grinding system processes to choose from, including open flow grinding, ordinary closed circuit grinding, pre-grinding, combined ...
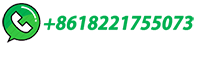