crushing grinding and screen analysis
Differences Between Grinding And Crushing. Difference between Crushing and Grinding. When making comparisons of the efficiencies of different grinding and crushing machines it is desirable to be able to estimate the work actually done in crushing the ore from a given size of feed to a given size of product, the screen analysis of both feed …
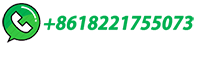