Beneficiation of Indian High Alumina Iron Ore Fines a …
Abstract Beneficiation of high alumina iron ore fines from Noamundi, India is studied for producing sinter/ pellet grade concentrate. The iron ore fine sample has a …
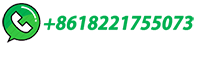
Abstract Beneficiation of high alumina iron ore fines from Noamundi, India is studied for producing sinter/ pellet grade concentrate. The iron ore fine sample has a …
Sintering is a thermal process (1300–1400°C) by which a mixture of iron ore, return fines, recycled products of the iron and steel industry (mill scale, blast furnace dusts, etc.), slag-forming elements, fluxes and coke are agglomerated in a sinter plant with the purpose of manufacturing a sintered product of a suitable chemical composition ...
At present, gravity separation equipments are prime concentrating units in the beneficiation of coal, iron ore, heavy mineral sand, gold, barite, fluorspar, tin, tungsten, etc. Beniuk et al. (1994) reported that majority of …
Huge quantity of raw chromite ore is being mined and beneficiated in various chrome ore beneficiation plants throughout the world to cater the customized needs of various ferro alloy plants. During mining and processing operations enormous quantities of fines are generated, which are of major concern from handling, storage and …
composition of iron ore fines. Co mpositionally, Indian iron ore fines contain hematite and goeth ite as major iron bearing min-erals. Gangue minerals are mostly alumina-silicate which re-mains inside the pores of goethite minerals in ultrafine size. However, some studies have focused on beneficiation of Indian iron ore fines and slimes using ...
950tph iron ore beneficiation wet processing project in South Australia. Learn more about this award-winning CDE and Simec Mining project. ... Ultra Fines Recovery ... The iron ore wash plant also removes clays from the feed material and the combined effect means the Fe content increases from between 43.4% and 52.7% in the feed to above 60% ...
The plant is designed to utilize the low grade fines available in the nearby vicinity of grade 58-60 fe. The beneficiated ore is utilised as feed for DRI, Sinter and Pellet plant. ... Effluent from the iron ore beneficiation …
to deliver fine iron ore beneficiation solutions With over 80 years' proven experience, we bring unrivalled expertise and the latest technologies to ... from first ore. The Iron Baron plant beneficates highly variable low-grade ore from a nominal 50% Fe to an Fe content of 64%. At full feed capacity the plant
The world's largest producers rely on Mineral Technologies for iron ore processing solutions. From Canada's Labrador Trough region, across India, Brazil and Africa, to Australia's iron rich Pilbara, our teams deliver …
2.4 Slimes of Iron ore 11 3. BENEFICIATION PLANT STUDY OF NOAMUNDI ... lumpy ore. Out of the fines resources about 2,543 million tons (22%) are medium grade ore, 39.9 million tonnes (1%) are high-grade and 17.7 million tons (1%) resources are of blue dust range. The residual are low grade, unclassified resources of lumps and fines or high, …
Characterization and beneficiation of dry iron ore processing plant reject fines of Khondbond region, India, was investigated. Different characterization techniques viz. size analysis, size-wise chemical and density analysis, X-ray diffraction analysis, sink-float analysis, thermo gravimetric analysis, scanning electron microscopy, and …
The potential iron loss in ore beneficiation of three hypothetical ores with a rich fraction consisting of haematite …
Barsua iron ore mines, a captive iron ore mines of Rourkela Steel Plant, has adopted Remco Jigs for the beneficiation of low-grade iron ore fines at a size range of …
Experiments have shown that it is possible to obtain a concentrate containing 65% iron, 1.8% alumina and 1.4% silica with an iron recovery of 80% from the tailings of Barsuan iron ore plant ...
Iron ore can be upgraded to a higher iron ore content through beneficiation This process generates iron ore filter cake which needs to be pelletized to be used in the steel making process. Also during the processing of high grade iron ores which don't need beneficiated, fines which are generated can be pelletized and used instead of being ...
Most of the high-grade hematite iron ores are typically subjected to simple dry processes of crushing and classification to meet the size specifications required for direct shipping ore (DSO). This involves multistages of crushing and screening to obtain lump (−31.5 + 6.3 mm) and fines (approximately −6.3 mm) products.
1.30 MTPA Iron Ore Beneficiation plant 0.80 MTPA Jigging plant for sinter feed . Low grade Iron Ore fines produced from the mine will be transported to the Hopper crusher located in mining lease area by dump trucks and after crushing to the desired size in the crusher will be transported to the beneficiation plant by a covered belt conveyor.
In the present study a detailed characterization followed by beneficiation of low grade iron ore was studied. The Run of Mine (R.O.M) sample assayed 21.91 % Fe, which is very low grade in nature.
The iron ore fines sample was collected fro m the spiral classifier overflow of a typical Iron ore beneficiat ion plant of Table 1. Specific Gravity of the different size fractions Noamundi, India. ... „„A study on developing the process flow sheet strategy. the beneficiation of Indian iron ore fines and slime using a. The XRD study ...
of iron ore from barges and preparation of sample for determining physical characteristics has been introduced. Taking into consideration the latest developments in iron ore industry and trade at national and international levels, the ores have been classified into two broad categories, namely, lumps and fines. For the purpose of
The haematite ore in South Africa is processed in a dry process to a HQ lump ore with 64 % iron content and a sintered fine ore with 63.5 % iron content. For fine ore beneficiation, wet processes are used. Capacity at the Minas Rio is to be increased from 26.5 Mta capacity to 28 Mta in the forthcoming years.
a sintering plant; however, the finer fines resulting from the beneficiation process cannot usually be processed in a sintering plant and must be agglomerated in a pelletizing plant. Therefore, a ... pelletizing plant. 1.2 Outline of iron ore production The production of iron and steel in China has increased dramatically. In response to the ...
The depletion of high grade iron ore resources make it inevitable to utilize the existing low grade iron ores/ fines/ tailings with proper beneficiation to meet the present specification and demand.
JSW Steel sinter plant receives iron ore fines of –10 mm size from Bellary – Hospet region which consist of 3 to 9% bigger than 10 mm and 30 to 35% smaller than 0.15 mm size …
The Kemi chromium mine is an open-pit mine with a waste rock to ore ratio of 5.5:1. At Kemi, the ore from the mine contains 11% iron and 25.5% Cr 2 O 3. After beneficiation, the concentrate contains between 35% Cr 2 O 3 in the coarse fraction (lumps) and 44% of Cr 2 O 3 in the fines. The process steps will be explained in the …
The critical area of concern in any chrome ore beneficiation plant is the grinding circuit followed by beneficiation circuit comprising gravity units such as wet shaking tables and spirals. The effectiveness of grinding circuit depends on the consistent feed quality. Any variation in feed reduces the performance of the subsequent unit …
Research regarding iron ore flotation began in 1931, demonstrating that reverse. cationic flotation is a very efficient method for beneficiating oxidised iron ores. This method can also. be ...
Though the iron ore fines are high in Fe (T) content i.e. 64.07%, alumina in the sample is 2.39, which is not as desired for blast furnace operation. Table 1 Chemical analysis of plant feed. Full size table. Table 2 Size analysis of plant feed. ... The Beneficiation plant is equipped with equipment like All Flux, HGMS, De-sliming …
Beneficiation plant employing heavy media drums, spirals, and heavy media cyclones at BHP Iron Ore's Mt Whaleback operation in the Pilbara region of Western Australia. ... Fig. 1.48 shows the fluctuation of the 62% Fe iron ore fines CFR price over the period January 2019 to October 2021, ranging from less than US$71 to US$233 a …
Beneficiate ore, improve yield, conserve mineral & develop sustainably. Quality of fines has to meet the technological requirement of customers in terms of size, desired lower …
حقوق النشر © 2024.Artom كل الحقوق محفوظة.خريطة الموقع