Crushers
All rock crushers can be classified as falling into two main groups. Compressive crushers that press the material until it breaks, and impact crushers using the principle of quick impacts to crush the material. ...
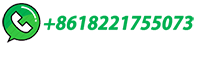
All rock crushers can be classified as falling into two main groups. Compressive crushers that press the material until it breaks, and impact crushers using the principle of quick impacts to crush the material. ...
Jaw crushers are mainly used in rock and stone quarries, sand and gravel, mining, construction and demolition recycling, construction aggregates, material grinding in various applications. The flywheel, knuckle plates, pitman, camshaft and drive motor of the jaw crusher create the crushing action and provide the energy required to crush the ...
what is a pitman on a rock crusher ; How does a Rock Crusher Work Jaw Crusher. Nov 22, 2021 The pitman is a twopiece annealed cast steel construction, with a cap designed for water cooling Bearing surfaces on both pitman and cap are babbitted and are joined together by four large forged steel bolts The elimination of excess bolts inherently found …
The Cone crusher mantle is one of the main components of the cone crusher, also known as the moving cone. The mantle is forged with new composite materials, which have the characteristics of super …
The moving jaw plate is mounted on the pitman, which is given a reciprocating motion. Crushing takes place when the pitman moves toward the stationary jaw. There are two main types of jaw …
The reduction ratio is driven by the Crusher Close Side Setting. The actual minimum safe closed side setting of a crusher will vary somewhat, for any given crushing machine, depending upon the character of the material, the amount of fines in the feed, and whether the crusher is being operated under choke-feed or regulated feed conditions. It …
The CrazyCrusher brand Rock Crusher is 100 percent steel, and it is 100 percent made in the U.S.A. by 100 percent Americans! The jaws are made of 3/8 steel, and the face has horizontal welds across them that not only help grip and pull down rock pieces, it also prevents wear on the actual jaws. On the moving jaw, vertical "teeth" were added to ...
The crusher is the workhorse of the hard rock crushing industry. A gyratory crusher uses a mantle that gyrates (rotates) within a cone shaped inner surface lined with wear resisting plates often called concaves. As the mantle gyrates within the crushing chamber, progressively approaching, and receding from, each element of the cone ...
The Rock Crusher is a Refinement Building. It turns Raw Minerals and Metal Ores into Sand and inefficiently produces Refined Metal. The Rock Crusher consumes 240 W of Power and requires Duplicant operation. It refines materials 100 kg at a time. 50 kg of material gets turned into Sand and 50 kg to the corresponding Refined Metal. One …
In the history of crushers, both chronologically, and by virtue of its standing in the field of heavy-duty crushing, the Blake jaw crusher stands first in the list. All of the large, heavy-duty primary crushers of the jaw type are built around the Blake principle which, for simplicity and brute strength, is unsurpassed by any mechanism thus far …
example, pitman eye protection protects the bearings and the pitman casting from impacts caused by really coarse feed, and it is also effortless to change. Even the main frame components are changeable thanks to the pinned and bolted design, prolonging the potential lifetime of the jaw crusher. C Series jaw crushers are modular
The heaviest part of a C200 jaw crusher for maintenance is the pitman assembly, which weighs about 40 tonnes and requires 5m of vertical space plus clearances for lifting. Although …
What Is A Pitman On A Rock Crusher,Patent US Pitman of a jaw crusher, jaw,Google 21 Feb 2013,A pitman of a jaw crusher comprising an upper part, which,Sep 25, 1956, Sep 9 . Jaw Crushers Metallurgist Mineral Processing Engineer. what is pitman in crushers .
First—those who have rock or ore tougher and more abrasive than most material. Second—the operators who've had difficulty with other designs of crushers. And finally—the operators who naturally buy the best—expecting their added investment to be written off in comparatively short time through lower operating a…
the crusher and scalp out fi nes. Primary gyratory crushers – ideally suited to all high-capacity primary hard rock crushing applications. Jaw crushers – we have more installed jaw crushers than anyone in the world. The lead-ing choice due to their high reduction ratio and heavy duty design. Cone crushers – capacities available to suit all
It is inevitable for crusher to get wear because of long-time crushing work, and all you can do is try your best to maximize its service life by regular check and timely maintenance. 1 Check whether the tooth peak to tooth valley is match with each other. 2 Regularly check whether the bolts and nuts have been tightened so you must ensure …
In a typical jaw crusher, two outer bearings located on either side of the main frame support an eccentric shaft, while two inner bearings support a movable jaw. These are commonly known as "Pitman" bearings. The reciprocating motion of the shaft moves the Pitman against a second, stationary jaw.
All jaw crushers come with off the shelf spherical roller bearings for both the pitman and the frame. The pitman bearings are oil lubricated and the frame bearings are grease lubricated from a central location to eliminate the need to shut down for lubrication. Flywheels One piece cast flywheels in 48" or 60" diameter sizes.
Cone crusher basics in 4 minutes. This is the starting point for understanding how cone crushers work – and how they can make your mine or quarry more productive. Elsewhere on the site you can find detailed information about all aspects of crushing and screening, but to make sense of these it helps to understand the basics of cone crushing.
Typically, the minimum setting on most primary crushers will be about 4 to 6 inches, as noted above. Compression-style jaw, cone, impact crushers, and gyratory crushers are most often appropriate as primary crushing …
The jaw crusher, also known as a toggle crusher, functions by compressing rock and stone between two jaw plates, one moving and one stationary. This mechanical pressure is achieved by two vertical jaws—one fixed, while the other reciprocates. ... The main components of a jaw crusher include the fixed jaw, the …
Jaw crushers are sometimes also referred to as "rock breakers''. A jaw crusher is one of the main types of primary crushers and it is used to decrease large size rocks by placing the rock into compression. ... With double-toggle jaw crushers, the pitman sits on a fixed non-eccentric control shaft that is mounted at the top of the crusher ...
A review on the design and operations challenges of a single toggle jaw crusher is presented. Strength and fracture toughness of the material to be crushed are intrinsic properties that determine ...
Stone Crushers or Rock Crushers are mainly used in the mining industry to reduce the size of stones into smaller rocks, gravel, sand, or rock dust. ... which is mounted on a pitman, is moving, and it has a reciprocating motion, and the other jaw is fixed & stays as it is. When the material runs between the two jaws, the jaws compress larger ...
what is pitman in crushers. The pitman, crusher frames, and bearing housings are made of high-quality cast steel 6 7 The right cavity design, C Series jaw crushers fits. More Price. Jaw Crusher 13y78. What Is A Pitman On A Rock Crusher, Expansion 13Y77 10 x 21 Thrust 13Y78 10 x 30, One month before the accident, the jaw crusher had been …
In the Dodge-type crusher, the movable jaw is pivoted at the bottom of the V. and thus it has a variable feed and a fixed discharge opening. This design also implies that the greatest amount of motion is at the top of the jaws. This type of crusher yields little oversize product and a great many fines. It also tends to "choke".
Our jaw pitman is made of high-quality cast steel and is propelled by massive cast steel or iron flywheels. We offer a wide range of replacement jaw pitman for jaw crushers, expertly machined to specification for fast, easy installation and good fit. Choose our jaw pitman to ensure a long trouble-free life, superior performance, and low wear costs.
Crusher Run gravel -- also known as 'Crush and Run', 'Crush N Run', 'Graded Aggregate Base' (GAB), or 'Aggregate Base Coarse' (ABC Stone) -- has perhaps even more useful applications than it does names it goes by. The material is most commonly used in home projects as a compactible sub-base material. It is a combination of coarse and fine ...
To compensate for wear on toggle plate, toggle seat, pitman toggle seat, and jaws additional shims must be inserted to maintain the same crusher opening. ... Rock breaker at the crusher station. As a …
jaw crusher. ×. 24 per page. The GrabCAD Library offers millions of free CAD designs, CAD files, and 3D models. Join the GrabCAD Community today to gain access and download!
حقوق النشر © 2024.Artom كل الحقوق محفوظة.خريطة الموقع