EVERY COMPONENT OF BALL MILL DETAILED & EXPLAINED
1.Axial/radial runout. 2.Alignment of the drive trains. 3.Uneven power splitting. 4.Centre distances variable. 5.Face load distribution. 6.Sealing of the girth gear. 7.Girth gear is through hardened only, fatigue strength is limited. -Dynamic behaviour. -A lot of individual rotating masses risk of resonance vicinities.
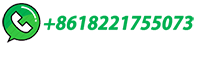