Newcrest mines data in the cloud for a $100m virtual goldmine
An early trial of using soft sensors in the Cadia mine involved assessing the capacity of crushed ore bins that sit underground. ... able to have a better understanding of the levels in those bins ...
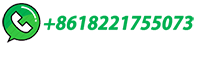