A critical review on energy use and savings in the cement industries
About 33% of energy is used for operating materials and 38% for clinker (38%) crushing and grinding equipment. Another 22% of the energy is spent for pyro-processing [20], [25], [26] . Fig. 3 shows that grinding (finish and raw grinding) consumes major share (i.e. 60%) of total energy consumption in a cement manufacturing process.
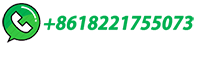