Beneficiation
Beneficiation includes crushing, grinding, gravity concentration and flotation concentration. Beneficiation is followed by processing activities such as smelting and …
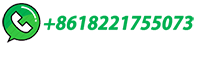
Beneficiation includes crushing, grinding, gravity concentration and flotation concentration. Beneficiation is followed by processing activities such as smelting and …
Abstract. Coal is a physical mixture of high carbon value coal and rejects. Coal beneficiation is nothing but the separation of these high carbon value coal from rejects (noncarbonaceous material) in a coal body. Although the theoretical knowledge of coal beneficiation is available aplenty in coal preparation books; it is essential that mineral ...
See more on magazine.primetals
WEBHence, the low-grade iron ore needs to be beneficiated to make the iron ore concentrate suitable for iron-making process. Thus, the main objective of …
Research highlights High tailing losses from the existing chromite plants (9–20% Cr 2 O 3). Accumulation of huge amount of low and sub-grade fines (10–30% Cr 2 O 3). Utilization of stockpiled tailings containing chromite values. Concentrate with required Cr 2 O 3 content and Cr/Fe ratio. Unrecoverable ultrafine chrome particles.
2. The jaw crusher crushes 50-230mm iron ore into the fine jaw crusher. Spiral washing machine is suitable for cleaning 0-50mm materials. 3. The fine jaw crusher crushes the material to 0-20mm. The vibrating screen sends the 0-20mm material into the ball mill, and the +20mm material returns to the fine jaw crusher.
The term separation in this case is synonymous with concentration. These functions are carried out within the constraints of …
Oct 1 2014. The beneficiation process can be defined as a treatment process of ore which results in a more concentrated form of the product. It is often used in the preparation of iron ore for smelting. This is an essential process as it helps improve the yield from a deposit of ore, thereby increasing the potential profits that can be obtained ...
Ore Benefication Plants Process This is a small scale gold ore processing plant that uses gravity concentration to separate the gold from the rock material It had a capacity of 1 2 ton per hour and was used in West Africa This particular mine had eluvial placer and small vein ore with veins averaging 2 3 inches in a stockwork formationMineral ...
It is rich in carbon and mineral matter. Coalification refers to the series of processes involved during the transformation of this organic vegetation into coal. The first step in transforming vegetation into coal is the formation of peat upon decay and decomposition of the dead plants through biological processes.
In general, iron ore beneficiation is done at the mining site. The concentrated iron ore is subsequently sintered or pelletized, depending on the grain size distribution, before it is charged to an ironmaking plant. …
Like the Sishen plant, the Mount Tom Price plant utilizes ferrosilicon as dense medium. A coarser grade (65D) is used for the drum plant and a finer grade (150D) for the cyclones. The efficiencies for the RTIO DMS plants also exhibit typically very small E p s—in the region of 0.05–0.1 kg/dm 3.
The ethanol precipitation procedure is repeated two to three times further, to purify the polysaccharide, and the solution dialyzed with double-distilled water. After dialysis, ECP is stored at low temperature (4°C). The concentration of ECP is determined by the phenol–sulfuric acid method [40]. Protein Analysis by UV-Visible Spectrophotometry
beneficiation. ore treatment. Also known as: concentration. Written and fact-checked by. The Editors of Encyclopaedia Britannica. Encyclopaedia Britannica's editors oversee subject areas in which they have extensive knowledge, whether from years of experience gained by working on that content or via study for an advanced degree.
Expand/collapse global location. 22.4: Beneficiation. Page ID. Ed Vitz, John W. Moore, Justin Shorb, Xavier Prat-Resina, Tim Wendorff, & Adam Hahn. Chemical …
Phosphate beneficiation plant In the treatment of phosphatic shales for recovery of phosphate, a simple low cost flexible flowsheet is highly desirable. Since all grades of ore from low to high P2O5 content may occur in a deposit it is important to consider the possibility of either mixing the ores or to segregate them into grades for …
The quality of Indian iron ore resources is generally good with high iron content and high percentage of lumpy ore. More than 85% of the hematite ore reserves are of medium- to high-grade (+62% Fe) and are directly used in blast furnace and in direct-reduced iron (DRI) plants in the form of sized lump ore, agglomerated sinter, and …
ore gravity concentration plant for sustainable development Y. Rama Murthy1 and S.K. Tripathy1,2 Synopsis India has limited resources of chromite. To optimally exploit this valuable and strategic raw material, numerous chrome ore beneficiation plants have been established. Most of these plants suffer chromite losses into the tailing.
Beneficiation plants are commonly associated with a mine. Once the phosphate ore is extracted, it typically undergoes a process of concentration …
Beneficiation is any process which removes the gangue minerals from ore to produce a higher grade product, and a waste stream. Beneficiation may involve physical or chemical processes. Often, as in the case of panning for gold, the desired ore or metal is denser than the gangue. The latter can be suspended in a stream of water and flushed …
Abstract. Investigations were carried out on lime stone rejects (−1 mm) generated at a lime stone washing plant in southern India. These rejects contain 12.09% CaO, 2.95% MgO, 10.73% Al 2 O 3, 4.99% Fe 2 O 3, 43.05% SiO 2 and 24.92% LOI. Mineralogical studies including SEM-EDAX, XRD, FTIR and TGA were conducted to …
The Fluorspar Beneficiation Problem Acid grade fluorspar which is in great demand by the chemical and aluminum industries, must contain at least 97.5% CaF2 with not more than 1.5% SiO2 and 0.5% Fe2O3. Often the Silica is limited to 1.2% with penalties starting at 1.0% SiO2. These limitations on grade and impurities require extremely close …
Chrome process equipment is wet type strong magnetic separator, and spiral chute (chrome spiral plant) of gravity separator. 3 Experimental results and discussion 3.1 Chrome magnetic separation process. The chrome raw ore is a flotation tail ore, which is mainly formed in the chromite, and the chromite is the target recovering …
Process optimization of a chrome ore gravity concentration plant for sustainable development. J. S. Afr. Inst. Min. Metall. [online]. 2020, vol.120, n.4, pp.26-268. ISSN 2411-9717. ... Most of these plants suffer chromite losses into the tailing. Decreasing these losses would not only improve the plant performance but also make the economics of ...
Concentration Concentration is increasing the percentage of the desired mineral in a given ore. Gravity Concentration: Gravity concentration is one of the oldest techniques (dates back to 3000 BC) that involves the separation of minerals with different gravity based on their relative movement in response towards the gravitational force. It may ...
primary form of mineral concentration for decades. Because of its high efficiency and low cost, gravity separation is always the first consideration in a flowsheet development program and always features in any flowsheet where there is sufficient differences between the specific gravity of the valuable and gangue minerals.
Before it is fed to the 4'x 8′ Peripheral Discharge Rod Mill, the minus ¼" chrome ore is removed from the grinding circuit by means of a 4'x 12′ Dillon Vibrating Screen. This minus ¼" product is then ready for …
Xstrata Coppers' Ernest Henry Mine (EHM) magnetite plants. The magnetite concentrator produces 1.2 Mt of magnetite concentrate per annum. The 3 MW M10000 installed IsaMill grinds the magnetite concentrate (with particle size ranging between 150 to 200 m) from the rougher magnetic separation
You've already forked sbm 0 Code Issues Pull Requests Packages Projects Releases Wiki Activity
Abstract. Choice selection and application variation of physical beneficiation techniques usually employed on heavy minerals (HMs) depends greatly …
In recent years, lead and zinc, emerge to become one of the most widely used non-ferrous metals for their growing demand in lead-acid batteries, galvanization, radio-active shielding, alloy, and pigments, etc. With continuous exploitation and expanding plant capacity, exhaustion of primary high-grade lead-zinc resources has already been …
حقوق النشر © 2024.Artom كل الحقوق محفوظة.خريطة الموقع